Additives Used in Plastic Manufacturing
Plastics are an integral part of modern life, used in a variety of applications ranging from packaging and automotive components to consumer products and medical devices. However, the base polymer used in the creation of plastic products often requires enhancements to meet specific performance criteria. This is where polymer additives come into play. Additives are substances added to plastics to achieve desired physical and chemical properties, improve performance, and ensure product longevity. This article explores various types of additives commonly employed in plastic manufacturing and their functions.
1. Plasticizers
Plasticizers are perhaps the most well-known additives in plastic manufacturing. They increase the flexibility and workability of plastics, especially polyvinyl chloride (PVC). By integrating plasticizers, manufacturers can create softer materials that are easier to mold and shape. Common plasticizers include phthalates; however, due to health concerns, there has been a shift towards using non-phthalate alternatives like citrates and adipates.
2. Stabilizers
During processing and throughout their lifespan, plastics can degrade due to heat, light, and moisture. Stabilizers are additives used to mitigate this degradation. Heat stabilizers prevent the decomposition of the polymer during processing, while UV stabilizers protect against ultraviolet radiation that can cause color fading and material brittleness. Common stabilizers include barium-cadmium compounds and organic UV absorbers, which extend the life of plastic products significantly.
3. Fillers
Fillers are materials added to plastics to increase volume, reduce production costs, and enhance certain properties. Common fillers include calcium carbonate, talc, and clay. These materials can improve the tensile strength and rigidity of the final product. Additionally, fillers can modify the thermal and electrical properties of plastics, making them suitable for specific applications. For instance, adding carbon black not only increases UV protection but also improves electrical conductivity.
additives used in plastic manufacturing
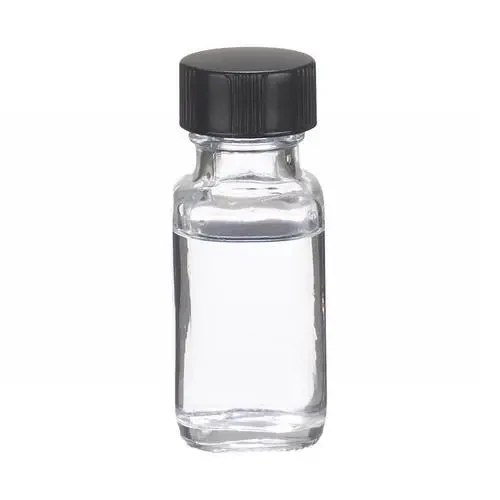
Color and aesthetics are critical aspects of plastic products, leading to the widespread use of coloring agents. Dyes and pigments are added to plastics to achieve various colors, enhancing their market appeal. Pigments are usually preferred over dyes because they are more stable and offer better outdoor durability. Titanium dioxide is a widely used white pigment that provides excellent opacity and brightness.
5. Antioxidants
Oxidative degradation can compromise the integrity of plastics, leading to discoloration and loss of mechanical properties. Antioxidants are additives that protect plastics from oxidative stress, especially during processing and service life. Common antioxidants include phenolic compounds and phosphites, which can significantly enhance the longevity of plastic products.
6. Flame Retardants
As safety regulations become stricter, flame retardants have become essential additives, especially for plastics used in electronics and automotive applications. These compounds inhibit combustion and reduce the flammability of plastic materials. While various flame retardants exist, including brominated and phosphorus-based products, environmental and health concerns have led to a shift towards the development of halogen-free alternatives.
7. Antimicrobial Agents
In applications where hygiene is paramount, such as in medical devices and food packaging, antimicrobial agents are added to inhibit the growth of bacteria and other pathogens. Silver ions and copper compounds are popular choices, providing long-lasting protection against microbial contamination.
Conclusion
In conclusion, the use of additives in plastic manufacturing is vital for enhancing the functionality and longevity of plastic products. From improving flexibility and durability to ensuring safety and aesthetics, these substances play a crucial role in the production process. As industry regulations and consumer demands evolve, the development of new and safer additives will remain a priority, ensuring that plastics continue to meet the challenges of modern applications while minimizing their environmental impact. Understanding the role of these additives not only benefits manufacturers but also aids consumers in making informed choices about the products they use in their daily lives.