Chemical Treatment for Chilled Water Systems
Chilled water systems are critical components in modern heating, ventilation, and air conditioning (HVAC) setups, providing efficient cooling for buildings and industrial processes. They operate by circulating water that has been cooled through a chiller, which absorbs heat from the building or process. While these systems are typically reliable, they can face several challenges, including scale formation, corrosion, and biological growth. To counter these issues, chemical treatment plays a vital role in maintaining the efficiency and longevity of chilled water systems.
Understanding the Challenges
1. Scaling As water evaporates and concentrates in systems, minerals such as calcium and magnesium can precipitate, forming scale on heat exchangers, cooling coils, and pipes. This buildup can severely limit heat transfer efficiency, leading to increased energy consumption.
2. Corrosion Metals in chilled water systems are susceptible to corrosion due to factors such as dissolved oxygen, low pH, and electrochemical reactions between dissimilar metals. Corrosion can lead to system leaks, equipment failure, and increased maintenance costs.
3. Biological Growth Biological organisms, including bacteria, algae, and fungi, can proliferate in chilled water systems. Not only can they cause fouling, leading to reduced system efficiency, but certain organisms can also introduce health risks, such as Legionella in cooling towers.
The Role of Chemical Treatment
Chemical treatment involves the systematic addition of specific substances to the chilled water to mitigate the challenges described above. These treatments commonly consist of scale inhibitors, corrosion inhibitors, and biocides. Implementing a well-designed chemical treatment program can lead to significant benefits.
1. Scale Inhibitors These chemicals work by interfering with the crystallization process of scale-forming minerals. Commonly used inhibitors include phosphonates and polyacrylic acids. By preventing scale formation, these chemicals help maintain heat transfer efficiency, reduce energy usage, and minimize downtime for cleaning and maintenance.
2. Corrosion Inhibitors To protect against corrosion, various inhibitors are employed depending on the system's metallurgy and water chemistry. Common types include chromates, molybdates, and amine-based compounds. These substances create a protective film on metal surfaces, reducing the rate of corrosion and thereby prolonging the lifespan of the equipment.
chemical treatment for chilled water system
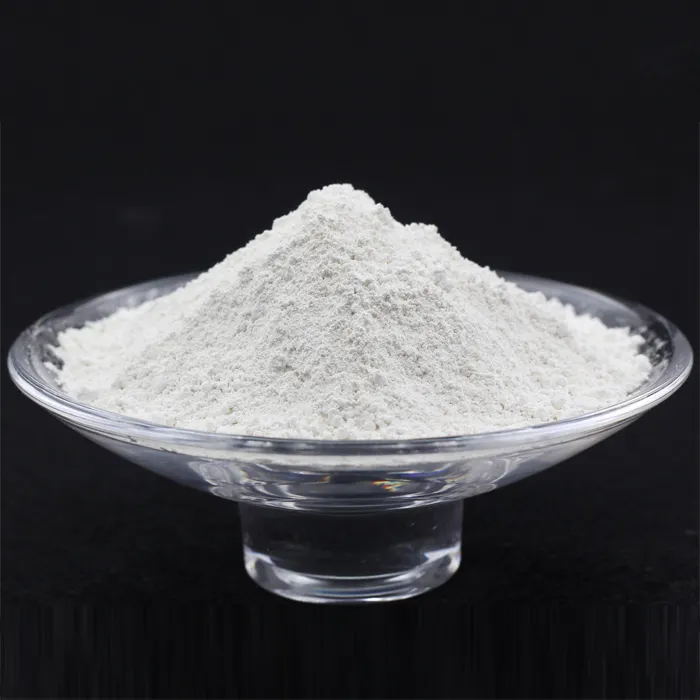
3. Biocides Effective control of microbial growth typically requires the use of biocides, which can be either oxidizing (e.g., chlorine, bromine) or non-oxidizing (e.g., isothiazolinones, quaternary ammonium compounds). Regular biocide application not only prevents biofouling but also addresses health risks associated with harmful organisms.
Implementation of a Chemical Treatment Program
An effective chemical treatment program should be tailored to the specific needs of the chilled water system. The following steps are generally involved
1. Water Quality Analysis Conducting regular water quality testing is essential for understanding the system's current condition. Parameters such as pH, conductivity, and the concentrations of specific ions (calcium, magnesium, and alkalinity) should be monitored.
2. Determining the Appropriate Chemicals Based on the analysis, the next step is to select the right combination of chemicals. A comprehensive approach may involve multiple treatments to address scale, corrosion, and biological growth simultaneously.
3. Monitoring and Adjusting Continuous monitoring of the system's performance and water chemistry is crucial. This data allows for adjustments in chemical dosages, ensuring optimal protection without over-treatment, which can lead to other complications.
4. Documentation and Compliance Maintaining detailed records of water quality tests, chemical treatments, and maintenance activities is essential for compliance with industry regulations and guidelines.
Conclusion
Chemical treatment for chilled water systems is an essential aspect of HVAC maintenance that can improve efficiency, extend equipment life, and ensure safe operation. By implementing a well-planned chemical treatment strategy, facility managers can mitigate the risks of scaling, corrosion, and microbial growth, ultimately leading to cost savings and enhanced system performance. Regular monitoring and testing, along with a tailored selection of chemical treatments, are vital for achieving the best outcomes in chilled water system management.