Chemical Treatment in Cooling Towers
Cooling towers play a critical role in various industrial processes, particularly in power generation, chemical manufacturing, and HVAC systems. They are integral for dissipating heat from the recirculating water systems, maintaining operational efficiency, and ensuring equipment longevity. However, the efficiency and reliability of cooling towers can be severely compromised by scaling, corrosion, and biological growth. To combat these challenges, chemical treatment strategies are employed to maintain optimal operating conditions.
Understanding Cooling Tower Functions
Cooling towers facilitate the heat exchange process by transferring excess heat from water to the atmosphere. They operate on the principle of evaporative cooling and are designed to enhance the cooling process by maximizing water surface area and air exposure. However, the cooling tower water is prone to various detrimental issues, such as algae growth, scale formation, and corrosion, which can lead to system inefficiencies, increased energy costs, and significant maintenance challenges.
Challenges Faced by Cooling Towers
1. Scaling Scaling occurs when dissolved minerals in the water precipitate and form deposits on system surfaces, including heat exchangers and pumps. Common minerals such as calcium and magnesium contribute to this problem. Scale buildup can severely restrict water flow, reduce heat transfer efficiency, and increase energy consumption.
2. Corrosion The metals used in cooling tower components, such as steel and copper, are vulnerable to corrosion, especially when exposed to oxygen and aggressive water chemistry. Corrosion not only weakens structural integrity but also generates metal flakes that can block flow paths and result in costly repairs.
3. Biological Growth Algae, bacteria, and other microorganisms can proliferate in the warm, moist environment of cooling towers. This biological growth can produce slime (biofilm) that further contributes to scaling and corrosion, leading to decreased efficiency and a greater risk of system failure. Moreover, certain bacteria, such as Legionella, can pose serious health risks.
Chemical Treatment Solutions
To mitigate these issues, chemical treatment programs are essential and typically include the following
chemical treatment in cooling tower
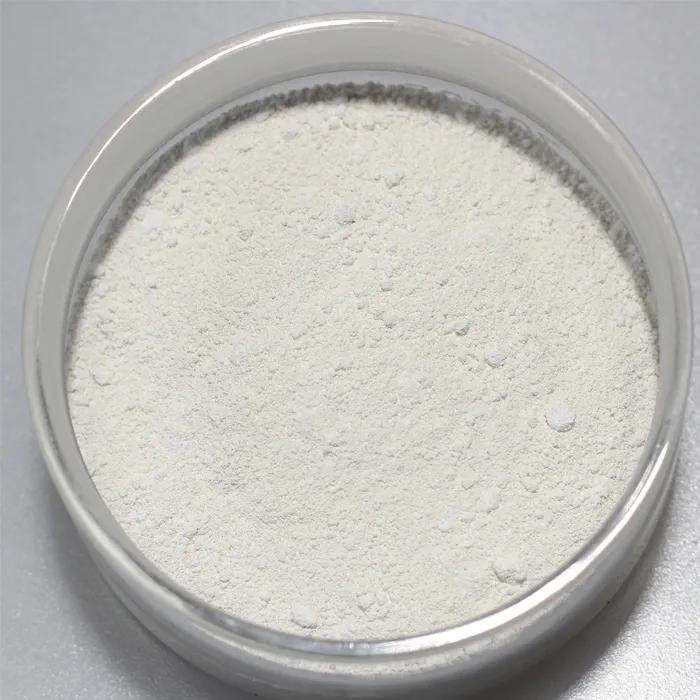
1. Scale Inhibitors These chemicals are designed to prevent the deposition of scale-forming minerals by modifying their properties, thereby keeping them in solution. Phosphate, polymeric dispersants, and sulfonates are commonly used scale inhibitors, which can help reduce the frequency of cleaning and maintenance while improving heat transfer efficiency.
2. Corrosion Inhibitors Corrosion inhibitors protect metal surfaces from oxidation and deterioration. They often function by forming a protective oxide layer or by sequestering harmful ions in the water. Commonly used inhibitors include azoles, phosphates, and organic acids. An effective corrosion management strategy can significantly extend the lifespan of cooling tower components.
3. Biocides Regular application of biocides is essential to control microbial growth that leads to biofouling. Chlorine, bromine, and non-oxidizing biocides are frequently used in cooling towers. These chemicals are effective at reducing microbial populations, which helps maintain system cleanliness and prevent health risks associated with pathogens like Legionella.
4. pH Control Maintaining proper pH levels is crucial for effective chemical treatment and overall system performance. pH control agents, such as sodium hydroxide or acetic acid, are utilized to adjust the water's acidity or alkalinity, creating an optimal environment for other treatment chemicals to perform effectively.
Implementing a Chemical Treatment Program
A successful chemical treatment program requires careful planning and monitoring. Facilities must conduct regular water tests to assess the effectiveness of the treatments and adjust dosing strategies accordingly. Moreover, integrating automated monitoring systems can enhance efficiency by providing real-time data on water quality parameters, allowing for immediate adjustments.
The choice of chemical treatments should be based on factors such as water quality, system design, and environmental regulations. Collaboration with chemical treatment specialists can help organizations develop a tailored program that meets specific operational needs while adhering to best practices for safety and environmental compliance.
Conclusion
In summary, chemical treatment plays an indispensable role in the effective operation and management of cooling towers. By addressing scaling, corrosion, and biological growth through well-designed chemical programs, industries can improve efficiency, reduce maintenance costs, and enhance the lifespan of their cooling systems. As technology advances and further regulations are introduced, ongoing innovation in chemical treatment strategies will remain crucial for sustainable industrial operations.