Chemicals Used in Boiler Feed Water Ensuring Efficiency and Longevity
Boilers are integral components in various industrial processes, providing steam and heat for operations. However, the effectiveness and longevity of a boiler system heavily depend on the quality of the feed water. The water fed into a boiler must be treated with specific chemicals to prevent a range of issues such as scaling, corrosion, and excessive foaming. This article explores the essential chemicals used in boiler feed water treatment, their functions, and their benefits.
1. Water Conditioning Agents
One of the primary chemicals used in boiler feed water treatment is water conditioning agents. These substances help in minimizing the scale formation inside the boiler. The most common water conditioning agents are phosphates and polymers. Phosphates, such as sodium phosphate, react with calcium and magnesium ions in the water to form insoluble compounds that can be easily removed. This minimizes the risk of scale buildup, which can significantly reduce boiler efficiency and damage its components.
Corrosion is a major challenge in boiler systems, primarily caused by oxygen and other dissolved gases in the feed water. To combat this, industries often use corrosion inhibitors. Common inhibitors include hydrazine and amines. Hydrazine effectively scavenges oxygen, thereby preventing oxidation of metallic surfaces. Amines, on the other hand, are volatile and can form a protective layer on metal surfaces, thus enhancing resistance to corrosion. By integrating these inhibitors, the lifespan of boiler components can be extended, reducing maintenance costs and downtime.
3. pH Adjusters
chemicals used in boiler feed water
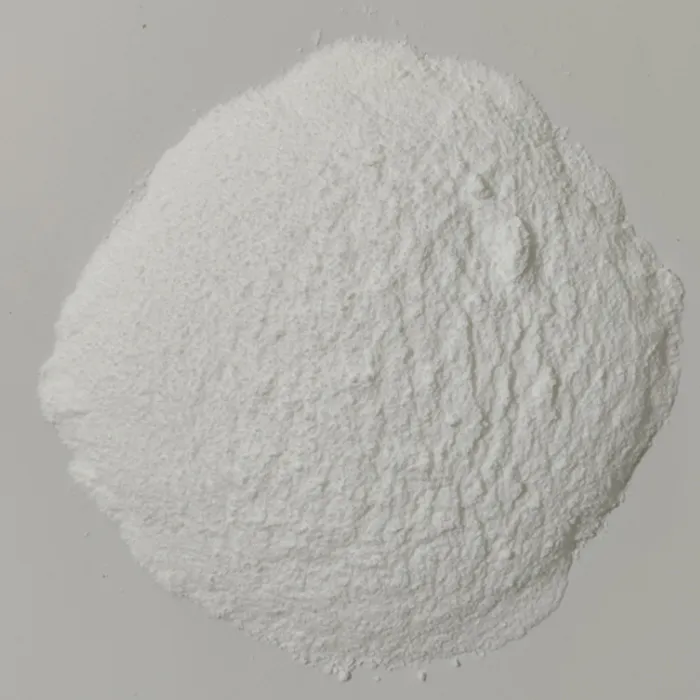
Maintaining the correct pH level in boiler feed water is crucial for preventing corrosion and ensuring proper chemical reactions. pH adjusters like sodium hydroxide are commonly used to raise the pH level of the water. A higher pH helps to minimize corrosion rates and enhances the effectiveness of phosphate treatment. Conversely, acetic or citric acids might be employed when the water's pH is too high. Proper pH management is essential for optimizing the performance of the boiler and ensuring safe and efficient operation.
4. Oxygen Scavengers
Oxygen scavengers play a pivotal role in preventing corrosion by eliminating dissolved oxygen from the feed water. Chemicals such as sodium sulfite and ascorbic acid are widely used for this purpose. They react with dissolved oxygen, forming non-corrosive byproducts. By reducing the amount of free oxygen in the water, these scavengers help maintain the integrity of boiler components, supporting a sustainable and efficient operation.
5. Anti-Foaming Agents
Foaming is another issue that can affect boiler performance, leading to water carryover into the steam system. Anti-foaming agents, such as polydimethylsiloxane, are employed to control and reduce foam formation. By stabilizing bubbles within the water, these agents help maintain a clear interface and ensure that steam quality remains high. Consequently, this contributes to improved energy efficiency and system reliability.
Conclusion
The treatment of boiler feed water with appropriate chemicals is essential for the efficient and safe operation of boiler systems. By utilizing water conditioning agents, corrosion inhibitors, pH adjusters, oxygen scavengers, and anti-foaming agents, industries can mitigate the risks associated with feed water quality. This proactive approach not only enhances the performance and longevity of boilers but also supports overall operational efficiency. Therefore, understanding and implementing effective water treatment practices is critical for industries relying on boiler systems.