Chemicals Used in Cooling Tower Water Treatment
Cooling towers play a crucial role in industrial and commercial processes by removing heat from equipment and rejecting it to the atmosphere. To ensure the efficiency and longevity of these systems, water treatment is essential. This article will explore the various chemicals used in cooling tower water treatment, highlighting their functions and importance.
1. Biocides
One of the primary challenges in cooling tower systems is the growth of microorganisms, including bacteria and algae. Biocides are chemicals that help control and eliminate these unwanted organisms. Common biocides used in cooling towers include chlorine, bromine, and proprietary formulations. Chlorine is a widely used disinfectant due to its effectiveness and cost efficiency. However, it can contribute to the formation of harmful byproducts. Bromine is often favored for its stability in high temperatures and can be used effectively in brominated cycles. Non-oxidizing biocides, such as isothiazolinones, are also popular as they provide longer-lasting control.
Corrosion is a significant concern in cooling towers, as it can lead to equipment failure and increased maintenance costs. To combat this, corrosion inhibitors are added to the water. These chemicals work by forming a protective film on the metal surfaces, reducing the rate of corrosion. Common corrosion inhibitors include phosphonates, molybdates, and zinc salts. Phosphonates are particularly effective in high pH environments and help maintain metal integrity under various operational conditions. Proper dosage and monitoring are crucial to ensure the effectiveness of these inhibitors.
3. Scale Inhibitors
chemicals used in cooling tower water treatment
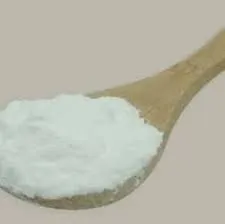
Water that evaporates in cooling towers can leave behind mineral deposits, leading to scale formation. These scales can clog systems and reduce heat transfer efficiency. Scale inhibitors are chemicals that prevent the precipitation of minerals such as calcium carbonate and calcium sulfate. Polymeric scale inhibitors, phosphate-based compounds, and phosphonates are commonly used for this purpose. They work by interfering with crystal growth, helping to keep minerals in a soluble state. Regular monitoring of water chemistry is essential to effectively manage scaling potential in cooling towers.
4. pH Adjusters
Maintaining the proper pH level is vital for optimal cooling tower operation. If the pH is too low (acidic), it can increase corrosion rates; if too high (alkaline), it can lead to scaling. pH adjusters like sodium hydroxide (to raise pH) and sulfuric acid (to lower pH) are commonly used. Regular testing and adjustment of pH levels help ensure the right conditions for the effective functioning of biocides, corrosion inhibitors, and scale inhibitors.
5. Anti-Foaming Agents
Foam can form in cooling towers due to surfactants and other materials in the water. Excessive foam can affect heat exchange and lead to overflow. Anti-foaming agents are added to control foam formation. These agents help reduce surface tension, enabling bubbles to collapse more easily. Polydimethylsiloxane (PDMS) is a typical choice for foam control in cooling water systems.
In conclusion, the treatment of cooling tower water is essential for maintaining system efficiency and longevity. By utilizing a combination of biocides, corrosion inhibitors, scale inhibitors, pH adjusters, and anti-foaming agents, operators can effectively manage water quality. Regular monitoring and adjustments are crucial to ensure the success of the treatment program, ultimately leading to reduced operational costs and enhanced system performance.