Functional Fillers for Plastics Enhancing Performance and Sustainability
Plastics are a fundamental part of modern life, playing crucial roles in a multitude of applications across various industries, from packaging and automotive to electronics and construction. However, the performance of plastics can sometimes be limited by their inherent properties. This is where functional fillers come into play. These materials are added to plastic formulations to enhance performance, reduce costs, and improve sustainability. By understanding the benefits and applications of functional fillers, industries can make informed decisions that enhance their material performance and overall product quality.
What are Functional Fillers?
Functional fillers are materials incorporated into polymer systems to enhance specific properties of the final product. Unlike traditional fillers which primarily serve to reduce cost or volume, functional fillers are selected for their ability to improve physical, chemical, or aesthetic performance. Some common types of functional fillers include
1. Mineral Fillers These include talc, calcium carbonate, and kaolin. They are used to enhance mechanical strength, thermal stability, and barrier properties. 2. Fibers Glass fibers, carbon fibers, and natural fibers improve tensile strength and impact resistance, making materials more durable. 3. Nanofillers Nanoclay and nanosilica enhance mechanical and thermal properties at very low loadings, taking advantage of the high surface area and unique aspect ratios of nanoparticles. 4. Additives These include flame retardants, antistatic agents, and UV stabilizers that improve durability and safety.
Benefits of Using Functional Fillers
The incorporation of functional fillers provides a wide array of benefits to plastic materials
1. Improved Mechanical Properties The addition of fillers can increase tensile strength, impact resistance, and flexural modulus, resulting in more robust products capable of withstanding demanding applications.
2. Cost Reduction By using functional fillers such as calcium carbonate, manufacturers can reduce the overall material cost while maintaining acceptable performance levels. This is especially relevant in commodity plastics where cost efficiency is crucial.
3. Enhanced Processing Characteristics Fillers can improve the flow properties of plastics during processing, allowing for easier molding and extrusion. This can lead to increased production efficiency and lower energy costs.
functional fillers for plastics
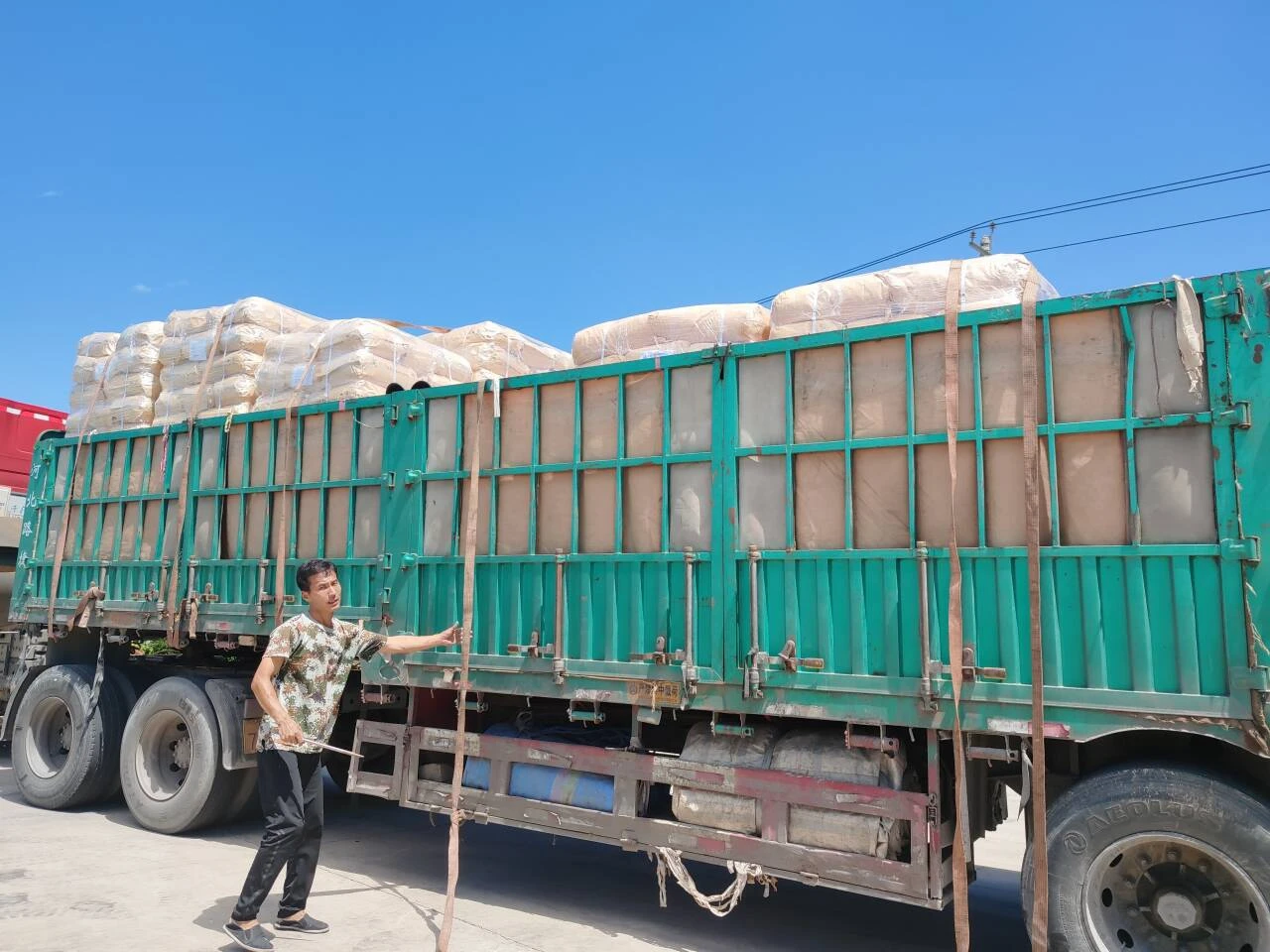
5. Versatility in Applications Functional fillers can be tailored for specific applications, providing custom solutions that meet unique performance requirements in industries ranging from automotive to consumer goods.
Trends in Functional Fillers for Plastics
The market for functional fillers in plastics is evolving rapidly due to the increasing demand for high-performance, sustainable materials. Several trends are driving innovation in this field
1. Bio-based and Sustainable Fillers There is a growing interest in using bio-based fillers made from renewable resources. These not only reduce environmental impact but also appeal to consumer preferences for sustainable products.
2. Nanotechnology The integration of nanofillers in plastics is gaining momentum. Researchers are developing new nanomaterials that enhance the mechanical, thermal, and barrier properties of plastics, promising superior performance with minimal material use.
3. Recycling and Circular Economy The focus on a circular economy is influencing the development of functional fillers derived from recycled plastics. This approach not only conserves resources but also provides a solution for managing plastic waste.
4. Advanced Functionalization Tailoring the surface properties of fillers can significantly enhance their compatibility and effectiveness when mixed with various types of polymers, leading to next-generation materials with customized performance.
Conclusion
Functional fillers play a pivotal role in enhancing the performance, cost-efficiency, and sustainability of plastics. As industries continue to innovate and seek out environmentally friendly solutions, the development and application of functional fillers will be paramount. By leveraging the advantages of these materials, manufacturers can create plastic products that meet the ever-evolving demands of consumers and the environment. Adopting functional fillers not only results in better performance but also aligns with the global push for sustainability in materials development, driving the future of plastics toward a more responsible and efficient path.