Understanding Plastic Masterbatch A Comprehensive Overview
In the heart of the modern manufacturing sector, the importance of plastic has become increasingly evident. From packaging materials to automotive components, plastics are versatile and pivotal to many industries. Among the various techniques used to enhance the properties of plastics, the use of masterbatches stands out as a significant innovation. Specifically, plastic masterbatch plays a crucial role in the production and performance of plastic products, making it an essential topic for anyone involved in material science or manufacturing.
What is Plastic Masterbatch?
Plastic masterbatch is a concentrated mixture of pigments and additives encapsulated within a carrier resin. This formulation is typically produced in pellet form and is used to impart specific colors, effects, or performance attributes to the end-product during the manufacturing process. The primary goal of using a masterbatch is to simplify the formulation process; rather than incorporating powders or liquid additives directly into the plastic, manufacturers can mix a relatively small amount of masterbatch into the base resin.
Types of Plastic Masterbatch
There are various types of masterbatches available, each serving distinct purposes
1. Color Masterbatch This type contains concentrated pigments that provide color to the plastic. Color masterbatches are available in a wide range of hues and can be tailored to meet specific customer requirements. The pigment concentration can vary depending on the desired final shade and the application.
2. Additive Masterbatch These masterbatches contain functional additives that enhance the properties of the plastic. Common additives include UV stabilizers, anti-oxidants, flame retardants, and anti-static agents. Each of these additives serves a particular purpose, such as improving durability, enhancing safety, or offering protection against environmental factors.
3. Special Effect Masterbatch As the name implies, this type includes components that provide special effects, such as metallic sheens, pearlescent finishes, or glow-in-the-dark capabilities. These masterbatches are increasingly popular in the packaging and consumer goods sectors, where aesthetic appeal is paramount.
Advantages of Using Plastic Masterbatch
1. Consistency and Quality Control Masterbatches ensure that the color and performance additives are homogeneously dispersed throughout the plastic. This uniformity results in consistent quality in the final products, reducing discrepancies that may arise from direct additization.
plastic masterbatch
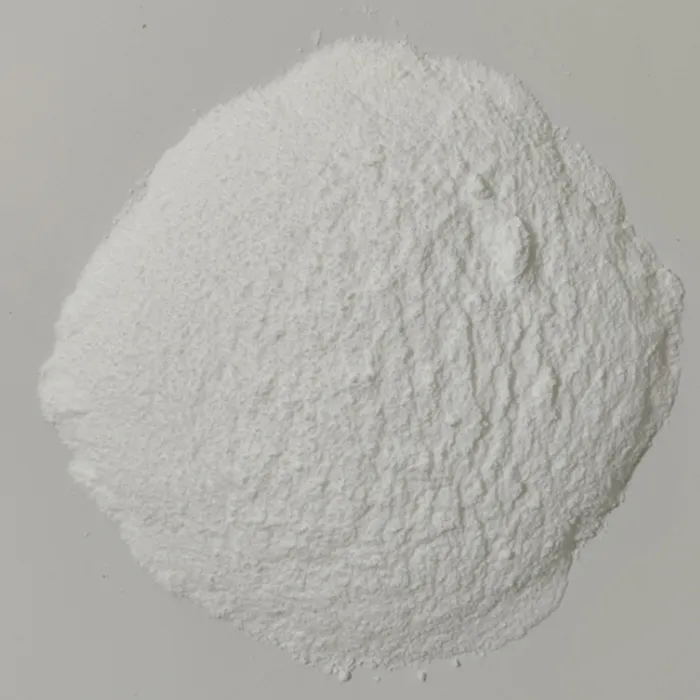
2. Ease of Use The pellet form of masterbatches makes them easy to handle, transport, and store. Furthermore, they can be easily mixed with various resins, allowing manufacturers to switch formulations without extensive retooling.
3. Cost-Efficiency By using plastic masterbatch, manufacturers can reduce costs associated with raw materials. Since masterbatches are concentrated, only small quantities are needed to achieve the desired effect, minimizing wastage and overall expenditure on additives.
4. Environmental Benefits Many masterbatches are designed with eco-friendliness in mind. This includes the development of biodegradable masterbatches and formulations that can enhance the recyclability of the final products.
Applications of Plastic Masterbatch
The applications for plastic masterbatch are vast and varied. Key industries benefiting from its use include
- Packaging Masterbatches are frequently used in the production of films, containers, and other packaging materials where color and functionality are critical.
- Automotive Within the automotive industry, masterbatches are employed to enhance parts for aesthetics as well as performance, such as resistance to UV light and impact.
- Consumer Products Toys, household items, and electronics all utilize masterbatches to achieve desired colors and functionalities.
Conclusion
The significance of plastic masterbatch in the realm of manufacturing cannot be understated. It not only enhances the aesthetic appeal and functional capabilities of plastic products but also streamlines production processes and reduces costs. As technology continues to evolve, so will the innovations in plastic masterbatches, promising even greater advancements in the future. For manufacturers aiming to improve product quality while maintaining sustainability, exploring the wide array of plastic masterbatch options is an essential step in modern production methodologies.