Boiler Water Chemistry An Essential Guide
Boiler water chemistry plays a pivotal role in the efficient and safe operation of industrial boilers. Proper management of the chemistry of water used in boilers can prevent issues such as scaling, corrosion, and foaming, which can lead to equipment failure and increased operational costs. Understanding the critical parameters of boiler water chemistry is essential for both operators and maintenance personnel.
At the heart of boiler water chemistry is the control of various chemical parameters, including pH, total dissolved solids (TDS), alkalinity, hardness, and specific ion concentrations. Each of these parameters must be carefully managed to ensure optimal boiler performance and longevity.
pH Control
One of the most critical factors in boiler water chemistry is pH. The pH level of boiler water typically should be maintained within a range of 10.5 to 11.5 to protect against corrosion and scaling. A pH that is too low can lead to acidic conditions, promoting corrosion of metal surfaces within the boiler. Conversely, excessively high pH levels can result in the formation of alkaline scales, particularly in high-pressure systems. Regular monitoring and chemical treatment, such as the addition of caustic soda or sodium phosphate, are often employed to maintain proper pH levels.
Total Dissolved Solids (TDS)
TDS refers to the concentration of dissolved substances in water, including minerals and salts. High levels of TDS can lead to scaling on heat transfer surfaces, reducing efficiency and increasing energy consumption. Steam purity can also become compromised, leading to carryover, which can affect downstream equipment. Routine blowdown, a process of removing a portion of concentrated water from the boiler, is essential for controlling TDS levels. Blowdown practices vary depending on the boiler type and operating conditions, and should be adjusted to maintain optimal performance.
Alkalinity and Hardness
boiler water chemistry pdf
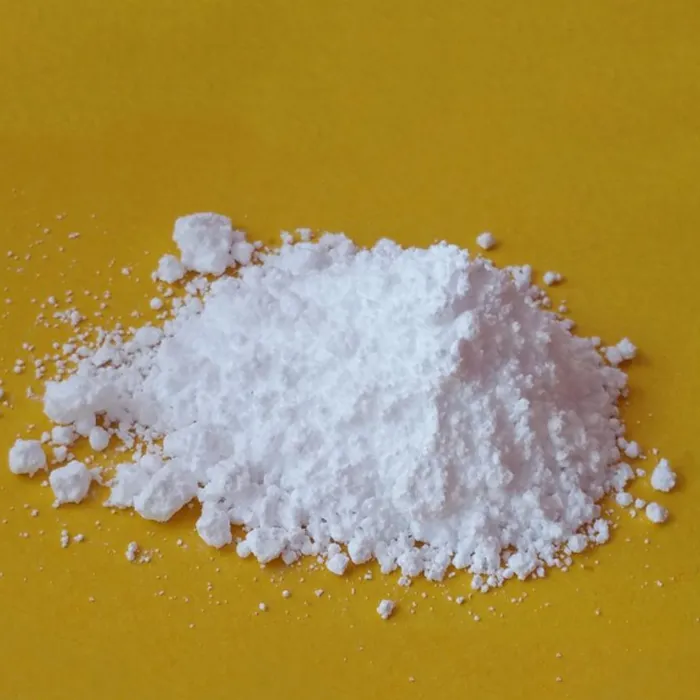
Alkalinity measures the ability of water to neutralize acids, primarily due to the presence of bicarbonates and carbonates. High alkalinity is generally favorable in boiler operations, as it helps prevent corrosion. However, excessively high alkalinity can contribute to foaming, which can lead to poor steam quality and equipment damage. Regular testing and adjustment of alkalinity are important to maintain balance.
Hardness, caused by calcium and magnesium ions, poses significant challenges in boiler water chemistry. Hard water can form scale deposits, particularly in high-temperature sections of the boiler. These deposits act as insulators, impeding heat transfer and increasing fuel consumption. To mitigate these effects, water softening processes, such as ion exchange, are commonly employed prior to boiler feedwater treatment, ensuring that hardness levels remain low.
Specific Ion Concentrations
In addition to TDS and hardness, monitoring specific ion concentrations is crucial in managing boiler water chemistry. Key ions of concern include chloride and sulfate, which can exacerbate corrosion rates in boiler systems. Chlorides, in particular, are known for their aggressive nature in promoting localized corrosion. Therefore, it is essential to limit chloride levels through effective water pretreatment and continuous monitoring.
Conclusion
Effective boiler water chemistry management is indispensable for optimizing performance and ensuring the longevity of boiler systems. By controlling parameters such as pH, TDS, alkalinity, hardness, and specific ion concentrations, operators can prevent common issues such as scaling, corrosion, and foaming. Consequently, this enhances the safety, efficiency, and reliability of boiler operations while minimizing operational costs.
Regular training and adherence to best practices in water chemistry management are essential for personnel involved in boiler operation and maintenance. Through diligent monitoring and proactive treatment, we can harness the full potential of our boiler systems while avoiding costly setbacks. As technology advances, the integration of automated monitoring systems and advanced chemical treatments will undoubtedly enhance our capacity to manage boiler water chemistry effectively, ensuring a sustainable and efficient future for industrial heating applications.