Understanding Chemical Dosing in Cooling Towers
Cooling towers are essential components in many industrial and commercial facilities, helping to dissipate heat from various processes. To maintain optimal performance and extend the lifespan of cooling systems, proper chemical dosing is crucial. This article explores the significance of chemical dosing in cooling towers, the types of chemicals used, and best practices for implementation.
Understanding Chemical Dosing in Cooling Towers
One of the main concerns in cooling tower operations is scaling, which occurs when minerals in the water precipitate and deposit onto heat exchange surfaces. This buildup can severely impede heat transfer, leading to higher energy consumption and premature equipment failure. To combat scaling, water treatment chemicals such as phosphonates and polyacrylates are commonly used. These agents inhibit the crystallization of scaling minerals, ensuring smooth system operation.
cooling tower chemical dosing pdf
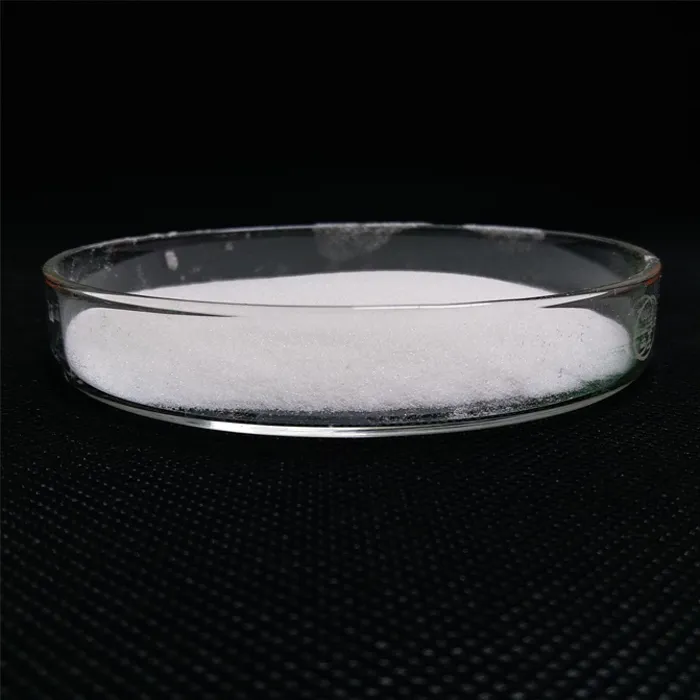
Corrosion is another significant threat to cooling towers. The presence of dissolved gases, such as oxygen, can lead to rust and deterioration of metal components. Chemical inhibitors, like molybdates and nitrites, are introduced to the water to form protective layers on metal surfaces, thereby mitigating corrosion. Selecting the right corrosion inhibitors is essential, as different metals react differently to various chemicals.
Biological growth, including algae and bacteria, can also pose challenges in cooling systems. Biofilms can form on surfaces, reducing efficiency and causing blockages. To address this issue, biocides like chlorine and bromine are frequently employed. These chemicals help control microbial populations, ensuring that the cooling water remains free of unwanted organisms.
Implementing a proper chemical dosing program involves careful monitoring and control. The concentrations of chemicals must be regularly tested to ensure effectiveness while avoiding overdosing, which can lead to adverse effects on both machinery and the environment. Many facilities utilize automated dosing systems that adjust chemical levels based on real-time data, optimizing the treatment process.
In summary, chemical dosing is a critical practice in maintaining the efficiency and longevity of cooling towers. By preventing scaling, corrosion, and biological contamination, facilities can enhance operational performance and reduce costs. Adopting best practices in chemical dosing not only protects the cooling systems but also contributes to a more sustainable approach to industrial cooling processes. As technology advances, the future of chemical dosing in cooling towers looks promising, with innovations aimed at improving effectiveness and minimizing environmental impact.