Chemical Foaming Agents for Plastics An Overview
Chemical foaming agents (CFAs) play a crucial role in the plastic industry, particularly in the manufacturing of lightweight materials with enhanced properties. These agents, which can generate gas during polymer processing, lead to the formation of a cellular structure within the plastic matrix. This not only reduces the overall weight of the product but also improves thermal insulation, sound absorption, and other mechanical properties. This article delves into the types, mechanisms, applications, and future trends of chemical foaming agents in plastics.
Types of Chemical Foaming Agents
Chemical foaming agents can be categorized into two primary types exothermic and endothermic agents.
1. Exothermic Foaming Agents These produce gas through a chemical reaction that is often initiated by heat. Common examples include azodicarbonamide (ADC) and sodium bicarbonate. Exothermic agents are favored for their ability to generate a larger amount of gas, which can result in a more pronounced foam structure.
2. Endothermic Foaming Agents These require external heat to produce gas. They often decompose at higher temperatures, releasing gases such as carbon dioxide and nitrogen. Examples include ammonium bicarbonate and some acid-carbonate combinations. Endothermic agents tend to create finer and more uniform cell structures, making them suitable for specific applications.
Mechanisms of Action
The mechanism by which chemical foaming agents work is relatively straightforward. During the processing of plastics—often involving extrusion or injection molding—the foaming agent decomposes under heat, producing gas bubbles. These bubbles become trapped within the polymer matrix, leading to the formation of a foam. The parameters that influence this process include the temperature, pressure, and shear rate during processing, as well as the compatibility of the foaming agent with the specific type of polymer being used.
The resulting foam can be classified as either open-cell or closed-cell. Open-cell foams have interconnected pores, which allow air and moisture to pass through, whereas closed-cell foams have sealed cells that provide better insulation and buoyancy. The choice between these types often depends on the desired application.
Applications of Chemical Foaming Agents
chemical foaming agents for plastics
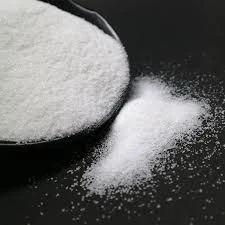
Chemical foaming agents are utilized across various industries due to their advantageous properties. Some of the key applications include
- Packaging Foamed plastics, such as expanded polystyrene (EPS) or polyethylene, are widely used in packaging materials, offering excellent cushioning and protection for fragile items.
- Construction Rigid foams, like those made from polyisocyanurate, provide insulation for walls, roofs, and floors. They enhance energy efficiency and contribute to sustainable building practices.
- Automotive Lightweight foamed plastics help reduce vehicle weight, improving fuel efficiency without compromising safety. Applications include interior components, bumpers, and sound dampening materials.
- Consumer Goods Products like foam mats, cushioning for electronics, and sporting equipment benefit from the lightweight and impact-resistant properties of foamed plastics.
Future Trends
The demand for lightweight materials is increasing, driven by environmental concerns and the need for energy efficiency. As a result, the market for chemical foaming agents is expected to grow significantly. Innovations such as bio-based foaming agents are on the rise, aiming to reduce the environmental impact of traditional chemical foaming agents derived from petroleum sources. Additionally, advancements in nanotechnology may lead to the development of new compounds that enhance the performance and functionality of foamed plastics.
Moreover, regulatory changes and sustainability trends will likely drive the development of more eco-friendly foaming agents. Manufacturers are also focusing on optimizing processing techniques to better control foam density and cell structure, ensuring that products meet specific performance requirements.
Conclusion
Chemical foaming agents are pivotal in transforming the properties of plastics, making them lighter, more efficient, and more versatile for various applications. As industries continue to seek sustainable and efficient solutions, the role of CFAs will become increasingly significant, paving the way for innovations that will shape the future of plastic materials. Understanding their types, mechanisms, and applications will allow manufacturers to leverage these agents effectively, ensuring continued advancements in the field of materials science.