Understanding Boiler Feed Water Chemical Treatment
Boiler feed water chemical treatment is a critical process in the operation of steam boilers and industrial heating systems. The quality of feed water directly influences the efficiency, reliability, and longevity of a boiler. Inadequate treatment can lead to a host of problems, including corrosion, scaling, and operational inefficiencies. Hence, it is vital to understand the significance of feed water treatment and the various chemicals involved in this process.
Importance of Boiler Feed Water Quality
The primary function of a boiler is to convert water into steam, which is then utilized in various industrial processes, including power generation, heating, and manufacturing. The water used in this process must be carefully treated to minimize impurities that can cause harm. Impurities such as dissolved oxygen, minerals, and other contaminants can lead to corrosion of boiler components, resulting in costly repairs and downtime.
One of the main objectives of boiler feed water treatment is to control the levels of total dissolved solids (TDS) and other harmful substances. High TDS levels can cause scaling, which reduces heat transfer efficiency and can lead to overheating and potential boiler failure. Furthermore, untreated water can create an environment conducive to microbiological growth, which can also compromise equipment integrity.
Common Chemicals Used in Treatment
The chemical treatment of boiler feed water typically involves several categories of chemicals, including oxygen scavengers, scale inhibitors, and pH adjusters
.boiler feed water chemical treatment
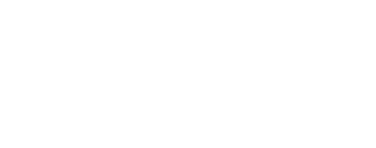
1. Oxygen Scavengers Dissolved oxygen is one of the major contributors to corrosion in boiler systems. Oxygen scavengers such as sodium sulfite and hydrazine are commonly added to the feed water to eliminate dissolved oxygen, thus protecting metal components from oxidative damage.
2. Scale Inhibitors Scale formation occurs when hard water minerals precipitate and stick to boiler surfaces. To prevent scaling, scale inhibitors such as polyacrylic acids, phosphonates, and chelating agents are used. These inhibitors work by interfering with the crystallization process of minerals, helping to keep them suspended in water rather than allowing them to settle on surfaces.
3. pH Adjusters Maintaining an appropriate pH level in the boiler feed water is crucial to preventing corrosion and scaling. Typically, a pH of around 10.5 to 11.5 is desired in boiler water. Chemicals such as sodium hydroxide or ammonia may be used to raise the pH, while organic acids may be employed to lower it, ensuring an optimal environment for boiler operation.
Monitoring and Control
Effective boiler feed water treatment requires continuous monitoring of water quality parameters. Regular testing for pH, conductivity, hardness, and TDS levels is essential to determine the effectiveness of the treatment chemicals. Furthermore, advanced monitoring systems equipped with automated controls can help in maintaining the desired water chemistry, ensuring that the boiler operates efficiently and safely.
Conclusion
In summary, boiler feed water chemical treatment is a fundamental aspect of boiler operation that cannot be overlooked. By implementing a comprehensive treatment program that includes the use of oxygen scavengers, scale inhibitors, and pH adjusters, industrial operations can significantly enhance the performance and reliability of their boiler systems. Not only does this lead to reduced operational costs associated with repairs and inefficiencies, but it also promotes safety and sustainability in industrial environments. Investing the time and resources into proper feed water treatment is crucial for any operation relying on boiler technology. This investment pays off in the long run, ensuring smooth operations and the longevity of equipment.