Additives Used in Plastic Manufacturing
Plastic manufacturing is an expansive field that has revolutionized various industries by providing versatile, durable, and cost-effective materials. However, the base polymers used in plastic production often require the incorporation of additives to enhance their properties and broaden their applicability. These additives play a crucial role in determining the final performance characteristics of the plastics, and their importance cannot be overstated.
Types of Additives
The additives used in plastic manufacturing can be categorized into several types, each serving distinct purposes
1. Stabilizers One of the primary concerns in plastic manufacturing is the degradation of materials due to exposure to UV light, heat, or oxygen. Stabilizers, such as antioxidants and UV stabilizers, are incorporated into the plastic mix to prevent discoloration and loss of mechanical properties during processing and service life. For example, hindered amine light stabilizers (HALS) are widely used to improve the longevity of outdoor plastics.
2. Plasticizers Plasticizers are essential for making rigid polymers more flexible and easier to process. They are particularly important in polyvinyl chloride (PVC) applications. By integrating plasticizers, manufacturers can produce materials that can be molded into complex shapes without compromising performance. Common plasticizers include phthalates, although health concerns have led to the exploration of alternative plasticizers like citrate esters and bio-based options.
3. Fillers Fillers are added to plastics to improve their mechanical properties, reduce production costs, and sometimes enhance thermal or electrical insulation. Talc, calcium carbonate, and glass fibers are just a few examples of fillers that are widely used. Incorporating fillers can provide additional strength and rigidity to the plastic, making it suitable for structural applications.
4. Flame Retardants With increasing fire safety regulations, flame retardants have become necessary additives for many plastic applications, particularly in electrical and electronic devices. These additives work by either enhancing the material's resistance to ignition or inhibiting the spread of flames once ignited. Common flame retardants include brominated compounds and phosphorus-based systems.
5. Colorants and Pigments Colorants are crucial in plastic manufacturing as they provide aesthetic appeal and brand differentiation. Dyes and pigments can be added to plastics to achieve specific colors and effects. Additionally, colorants can also offer UV resistance, providing extended durability to colored plastics.
6. Anti-static Agents In various industries, especially electronics, plastic components must be treated to prevent static electricity buildup, which could damage sensitive equipment. Anti-static agents are added to the plastic formulation to manage static discharge effectively.
Benefits of Additives
additives used in plastic manufacturing
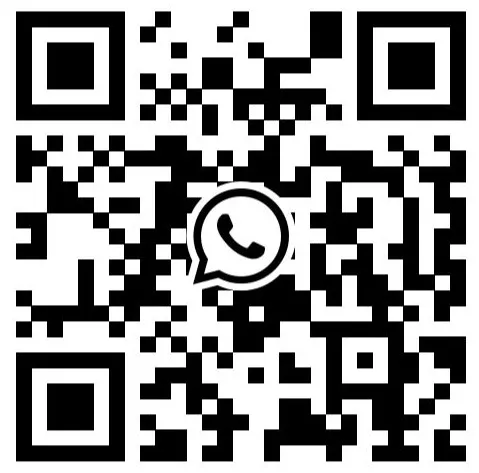
The incorporation of additives into plastic manufacturing offers several benefits
- Enhanced Performance Additives improve properties such as flexibility, impact resistance, and thermal stability, enabling plastics to perform better in their intended applications.
- Cost Efficiency By using fillers and other cost-effective additives, manufacturers can reduce production costs without sacrificing quality.
- Customization Additives allow manufacturers to tailor plastics to meet specific requirements, whether for strength, flexibility, color, or resistance to environmental factors.
- Regulatory Compliance Additives such as flame retardants help products meet safety standards, thus ensuring compliance with regulations and protection for consumers.
Challenges and Future Trends
Despite their benefits, the use of additives in plastics also presents challenges. Environmental concerns regarding certain additives, particularly plasticizers and flame retardants, have prompted extensive research into safer alternatives. Additionally, the recycling of plastics containing various additives can complicate the recycling process, as different additives can interact in unpredictable ways.
The future of additives in plastic manufacturing lies in the development of sustainable and eco-friendly alternatives. Bio-based additives, biodegradable polymers, and non-toxic formulations are gaining traction as industries strive for greener solutions. Furthermore, innovations such as nanotechnology may enhance the effectiveness of additives while minimizing their environmental footprint.
Conclusion
Additives are integral to plastic manufacturing, enhancing performance characteristics and expanding application possibilities. As industries evolve and sustainability becomes a priority, the focus will be on developing safer, more efficient, and environmentally friendly additives, paving the way for the future of plastic materials. The balance of performance, cost, and environmental impact will remain at the forefront of research and development in this dynamic field.