The Role of APIs in Modern Manufacturing
In today's rapidly evolving industrial landscape, the integration of technology into manufacturing processes has become imperative for companies seeking to enhance efficiency, productivity, and innovation. One pivotal development in this realm is the adoption of Application Programming Interfaces (APIs). APIs facilitate seamless communication between different software applications, enabling manufacturers to streamline operations, improve data accessibility, and foster collaboration across various sectors.
Enhancing Interconnectivity
Manufacturers often rely on numerous software systems to manage different facets of production, from supply chain management to quality control. APIs serve as the glue that binds these disparate systems together. By providing standardized protocols for data exchange, APIs allow for real-time communication between systems, which is crucial for making informed decisions quickly. For instance, an API can connect inventory management software with production systems, ensuring that materials are available when needed, thus reducing downtime and boosting efficiency.
Data Utilization and Analytics
In the age of Big Data, the ability to harness and analyze information is a significant competitive advantage. APIs enable manufacturers to extract data from various sources, such as IoT devices, ERP systems, and customer feedback channels. By aggregating this information, companies can gain valuable insights into production processes, identify bottlenecks, and track performance metrics. This level of data utilization allows manufacturers to implement data-driven strategies, optimize workflows, and foresee maintenance needs before equipment failures occur, ultimately leading to reduced costs and improved quality.
Facilitating Innovation
api for manufacturing
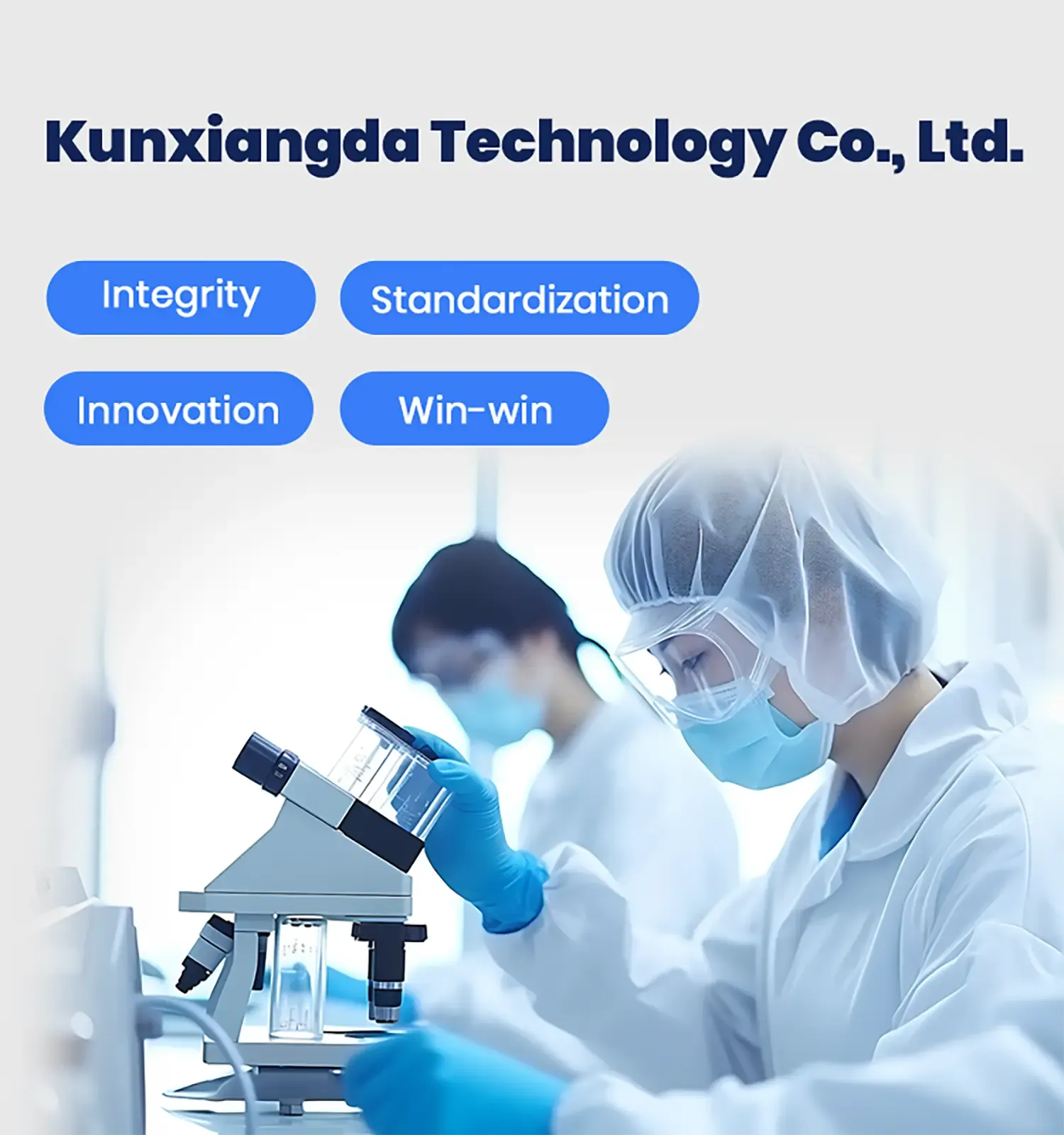
The manufacturing industry is witnessing a shift towards smart manufacturing systems characterized by automation, AI, and machine learning. APIs play a crucial role in enabling these technologies to function cohesively. For example, a manufacturer looking to implement AI-driven predictive maintenance can use APIs to connect their machinery's monitoring systems with analytical tools. This connectivity allows for advanced algorithms to analyze performance data in real-time, leading to more accurate maintenance forecasts and less unplanned downtime.
Moreover, APIs open the door for collaboration between manufacturers and technology providers. Third-party developers can create specialized applications that cater to specific manufacturing needs, further promoting innovation. This ecosystem encourages manufacturers to adopt new technologies rapidly, enabling them to stay ahead of the competition.
Personalization and Customer Engagement
APIs also enhance customer engagement by facilitating personalized experiences. For instance, manufacturers can leverage APIs to integrate customer relationship management (CRM) systems with production data. This integration allows for a better understanding of customer preferences and demand patterns, enabling manufacturers to tailor their offerings accordingly. As a result, companies can improve customer satisfaction and foster loyalty, which is essential in today’s competitive market.
Conclusion
The integration of APIs into the manufacturing sector is not merely a technological upgrade; it represents a fundamental shift in how companies operate. By enhancing interconnectivity, improving data utilization, fostering innovation, and personalizing customer interactions, APIs are transforming traditional manufacturing into a more agile and responsive industry. As manufacturers continue to embrace digital transformation, the strategic use of APIs will be crucial for driving efficiency and maintaining a competitive edge in the global market. The journey towards a more connected and intelligent manufacturing paradigm is just beginning, and APIs will undoubtedly play a central role in shaping its future.