The Role of Amine Injection in Boiler Feed Water Treatment
Boilers are essential components in various industrial processes, providing steam for heating, power generation, and other applications. The efficiency and longevity of a boiler largely depend on the quality of the feed water used. One of the most effective methods for ensuring the integrity of boiler systems is the injection of amines into the feed water. This article explores the significance of amine injection in boiler feed water treatment, its benefits, and the mechanisms involved.
Understanding Boiler Feed Water
Boiler feed water is the water that is supplied to a boiler for the generation of steam. If the water supplied to the boiler is not properly treated, it can lead to several issues, including scale formation, corrosion, and reduced efficiency. These problems can significantly affect the performance of the boiler and lead to increased maintenance costs and downtime.
Why Use Amines?
Amines are organic compounds derived from ammonia by replacement of one or more hydrogen atoms with hydrocarbon groups. When used in boiler feed water, amines serve as effective treatment chemicals for the prevention of corrosion in the steam and condensate systems. The two primary types of amines used in this context are neutralizing amines and filming amines.
1. Neutralizing Amines These amines, such as morpholine and diethylaminoethanol, primarily work by neutralizing the acidity in the water. By maintaining a higher pH level, they help protect the boiler and piping systems from acidic corrosion. This is crucial, particularly in systems that can become acidic due to various chemical reactions.
2. Filming Amines These compounds, such as aminoethylpiperazine, create a protective film on metal surfaces within the boiler. This film acts as a barrier between the metal and the water, reducing the risk of corrosion. The thin layer of amine helps to seal any micro-cracks or imperfections in the surface, further enhancing protection.
Benefits of Amine Injection
The injection of amines into boiler feed water offers several notable benefits
amine injection boiler feed water
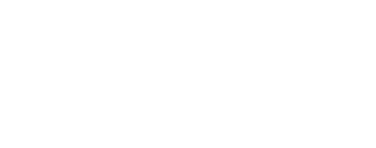
- Corrosion Control The primary advantage of amine injection is its ability to significantly reduce corrosion rates in the boiler and associated piping systems. This leads to extended equipment life and decreased maintenance requirements.
- Improved Heat Transfer By minimizing scaling and corrosion, amine treatment helps maintain the efficiency of heat transfer within the boiler. This results in reduced energy consumption and lower operational costs.
- Enhanced Safety With reduced corrosion and scale buildup, the risk of boiler failures and emergencies decreases, contributing to a safer operating environment.
- Cost-Effectiveness Although there is an upfront cost associated with amine treatment, the long-term savings from avoided repairs, prolonged equipment life, and increased operational efficiency often outweigh these initial expenses.
Implementation Considerations
While the benefits of amine injection are significant, careful consideration must be given to the specific type of amine, its concentration, and the conditions of the boiler system. Factors like water chemistry, operational temperature, and pressure must be taken into account to optimize the treatment process.
Additionally, regular monitoring and adjustment of the amine concentration may be necessary to ensure consistent performance and efficacy. An effective monitoring program will help in identifying any changes in the system and allow for prompt adjustments to maintain optimal conditions.
Conclusion
Amine injection plays a crucial role in the treatment of boiler feed water, addressing corrosion and inefficiencies that can arise from poor water quality. By implementing a robust amine treatment program, industries can enhance the reliability, safety, and efficiency of their boiler systems. As technology continues to advance, the potential for improved amine formulations and applications will provide even greater benefits to industrial operations worldwide.