Chemical Treatment in Cooling Towers Ensuring Efficiency and Longevity
Cooling towers are critical components in many industrial cooling systems, used extensively in power plants, manufacturing processes, and HVAC systems. Their primary purpose is to dissipate excess heat from processes through evaporation, enabling equipment to operate efficiently and safely. However, the efficiency and longevity of cooling towers can be significantly affected by various factors, including the quality of the water that circulates through them. This is where chemical treatment comes into play, serving to protect the system against scaling, corrosion, and biological growth.
Importance of Chemical Treatment
Chemical treatment in cooling towers is crucial for maintaining optimal performance. Cooling water is often sourced from natural bodies such as rivers or lakes, containing impurities that can lead to various problems. Without a proper chemical treatment program, these impurities can cause scaling on heat exchange surfaces. Scaling occurs when dissolved minerals, primarily calcium and magnesium, precipitate out of the water as it evaporates, forming deposits that hinder thermal efficiency. A well-designed chemical treatment regime helps to inhibit scaling, ensuring effective heat transfer and energy efficiency.
Moreover, corrosion is another major concern in cooling towers. The materials used in their construction, typically metals like steel or copper, can react with the circulating water, leading to deterioration over time. Corrosive effects are exacerbated by low pH levels and oxygen content in the water. Chemical treatments, such as the addition of corrosion inhibitors, help to form a protective barrier on metal surfaces, significantly extending the operational lifespan of the cooling system.
Biological growth, including algae, bacteria, and fungi, poses another risk to cooling towers. Not only can these organisms compromise water quality and efficiency, but they can also lead to health and environmental hazards. For instance, organisms like Legionella bacteria can flourish in improperly treated water, posing serious health risks. Chemical biocides, such as chlorine or bromine, are often utilized in cooling tower systems to control microbial growth. Regular monitoring and adjustment of biocide concentrations are essential to ensure the effectiveness of these treatments.
Types of Chemical Treatments
chemical treatment in cooling tower
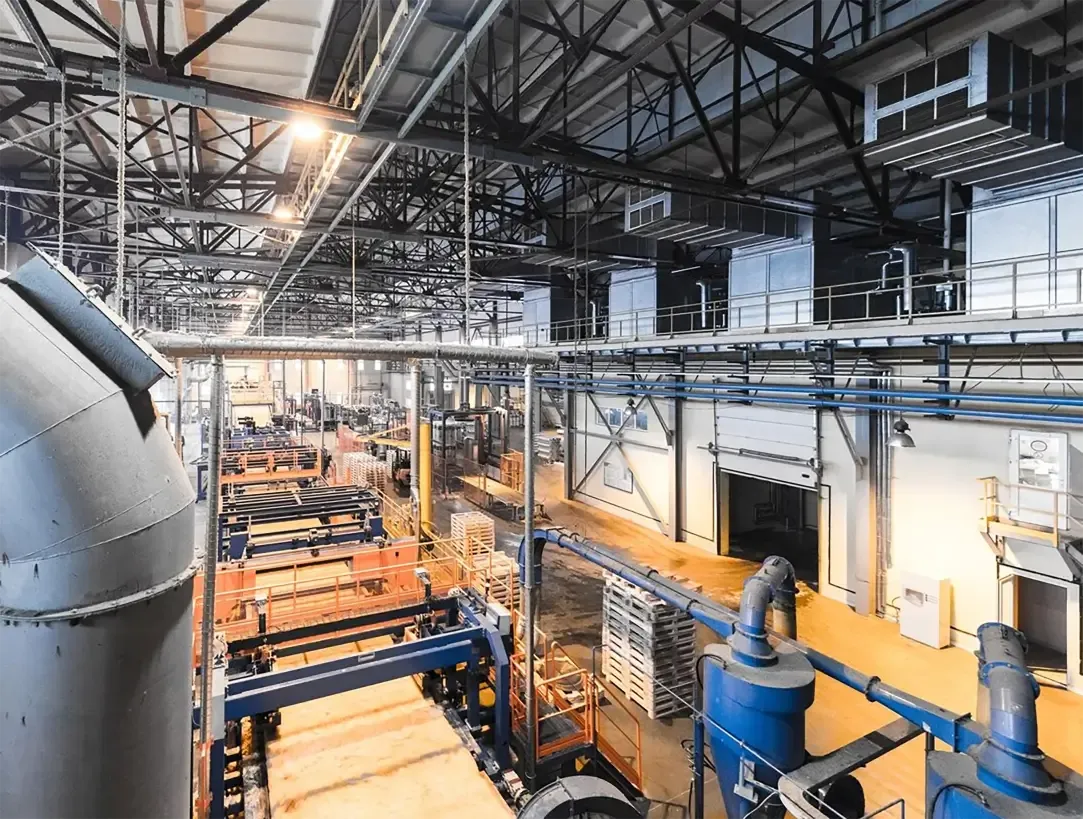
Chemical treatments in cooling towers can be broadly categorized into three main types scale inhibitors, corrosion inhibitors, and biocides
.1. Scale Inhibitors These chemicals, typically phosphonates or polyacrylates, work by preventing the crystallization of scale-forming minerals. They keep these minerals in a soluble state, thus reducing the likelihood of scaling on heat exchange surfaces.
2. Corrosion Inhibitors Commonly used corrosion inhibitors include amine-based compounds and phosphates. These chemicals react with the metal surfaces to form protective films, making them less susceptible to chemical attack from the cooling water.
3. Biocides These can be categorized into oxidizing and non-oxidizing agents. Oxidizing biocides, such as chlorine and chlorine dioxide, are effective at quickly reducing microbial populations. Non-oxidizing biocides, like isothiazolone compounds, offer prolonged effectiveness and are often used as part of a comprehensive water treatment plan.
Conclusion
Implementing an effective chemical treatment program is essential for maintaining cooling tower efficiency and longevity. By targeting scaling, corrosion, and biological growth, these treatments help ensure optimal performance, reduce maintenance costs, and enhance system durability. Regular water testing and monitoring, coupled with a well-planned chemical addition strategy, can significantly improve the reliability and efficiency of cooling tower operations.
As industries continue to face scrutiny over their environmental impact and water resource management, maintaining effective cooling tower operations through chemical treatment will not only help in compliance with regulations but also contribute to sustainable practices overall. A thorough understanding of the specific needs of each cooling system, alongside the appropriate use of chemical additives, will ensure that cooling towers remain valuable assets in the quest for efficient and sustainable industrial processes.