Chemical Use in Cooling Towers Importance and Best Practices
Cooling towers are essential components in many industrial and commercial facilities, serving as heat exchangers that dissipate excess heat to the atmosphere. They are widely used in power plants, petrochemical industries, HVAC systems, and various manufacturing processes. To enhance efficiency and prolong the life of cooling systems, various chemicals are used in cooling towers. Understanding these chemicals' roles, applications, and best practices is crucial for optimal performance and environmental compliance.
The Role of Chemicals in Cooling Towers
The primary purpose of chemicals in cooling towers is to maintain water quality and prevent issues like scaling, corrosion, and biological growth. Each of these problems can severely impact the efficiency of the cooling system and lead to increased operational costs.
1. Scale Inhibitors As water evaporates in cooling towers, it can lead to mineral deposits, or scaling, on the heat exchange surfaces. Scale reduces heat transfer efficiency and can lead to equipment damage. Scale inhibitors are added to prevent mineral deposits by interfering with the crystallization process. Common scale inhibitors include phosphonates and polyacrylic acid.
2. Corrosion Inhibitors The metals used in cooling towers are subject to oxidation when exposed to water and air. Corrosion can compromise structural integrity and result in costly repairs. Corrosion inhibitors, such as chromates, molybdates, and organic inhibitors, are dosed into the water to form protective films on metal surfaces, thereby reducing corrosion rates.
3. Biocides With stagnant water in cooling systems, algal and bacterial growth can occur, leading to biofilm formation. This biological growth can cause fouling, reducing system efficiency and creating health risks, such as Legionnaires' disease. Biocides, including chlorine, bromine, and non-oxidizing biocides, are used to eliminate or control microbial populations.
4. pH Control Agents The pH of water in a cooling tower plays a significant role in the effectiveness of both corrosion and scale inhibitors. Typically, a balanced pH range of 6.5 to 8.5 is targeted. pH control agents, such as sulfuric acid or sodium hydroxide, may be added to adjust the acidity or alkalinity of the water.
Best Practices for Chemical Use
chemical used in cooling tower
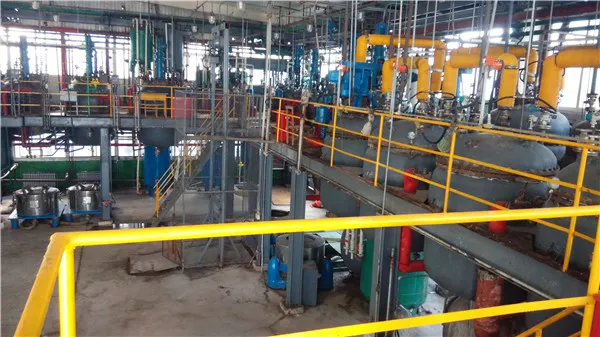
To maximize the effectiveness of chemicals in cooling towers and ensure environmental compliance, several best practices should be followed
- Regular Testing Routine water quality testing is essential to monitor parameters like pH, conductivity, and the concentrations of specific chemicals. This testing helps in adjusting dosages and maintaining optimal conditions for cooling system operation.
- Appropriate Dosing The effectiveness of chemical treatments depends heavily on the correct dosages. Over-treatment can lead to increased costs and environmental hazards, while under-treatment can cause operational issues. Following manufacturer's guidelines and onsite testing is crucial for effective dosing.
- Environmental Considerations Many cooling tower chemicals can have environmental impacts if not handled properly. Therefore, selecting eco-friendly biocides and corrosion inhibitors can help reduce the environmental footprint. Additionally, facilities should adhere to local regulations regarding chemical use and discharge.
- Maintenance and Monitoring Regular maintenance of cooling tower systems and the associated chemical feed systems is essential. Preventive maintenance schedules should include regular inspections of chemical storage, pump operations, and monitoring chemical feed rates to ensure systems operate without interruption.
- Training and Safety Personnel involved in the handling and application of chemicals should be adequately trained on safety protocols, proper handling techniques, and emergency procedures. This reduces the risk of accidents and ensures a safe working environment.
Conclusion
Effective chemical management in cooling towers is critical for operational efficiency, cost reduction, and environmental compliance. By understanding the different types of chemicals used, their roles, and implementing best practices, facilities can optimize their cooling tower operations while minimizing risks and maintaining high standards of safety and efficiency. As industries continue to evolve, so too will the approaches to chemical use in cooling towers, underscoring the need for ongoing research and adaptation to new technologies and regulations.