The Significance of Q10% in Advanced Manufacturing Technologies
In recent years, the landscape of advanced manufacturing has been revolutionized by the integration of sophisticated technologies and methodologies aimed at optimizing production efficiency and product quality. Among the myriad concepts in this domain, the term Q10% emerges as a significant metric that encapsulates both quality assurance and process efficiency. Understanding Q10% and its implications in the context of advanced manufacturing can provide critical insights into achieving operational excellence.
Understanding Q10%
Q10% refers to a statistical quality control measure that denotes the proportion of products meeting quality standards at a 10% improvement threshold. In essence, it signifies that 10% of the production process needs to meet a specific quality criterion without deviation, ensuring that the majority of products produced are of high standard. By implementing Q10% protocols, manufacturers can refine their processes to minimize defects and enhance overall product reliability. This metric becomes particularly relevant in industries like automotive and aerospace manufacturing, where precision and safety are paramount.
The Role of Technology in Achieving Q10%
The advent of Industry 4.0 technologies—such as the Internet of Things (IoT), artificial intelligence (AI), and big data analytics—has significantly bolstered manufacturers’ efforts to achieve Q10%. These technologies facilitate real-time monitoring of production processes, enabling manufacturers to respond swiftly to any anomalies that could impact product quality. For example, IoT sensors can track temperature, pressure, and other critical variables during production, ensuring that they remain within specified limits. If deviations occur, immediate corrective actions can be implemented, aligning with the Q10% ethos of maintaining high quality.
Moreover, AI algorithms can analyze data from previous production runs to predict potential defects, optimizing processes proactively. Such predictive analytics not only helps in maintaining the Q10% standard but also contributes to reduced waste and lower operational costs. By harnessing technology, manufacturers can establish a culture of continuous improvement that is essential for sustaining quality benchmarks.
q10 et pqq
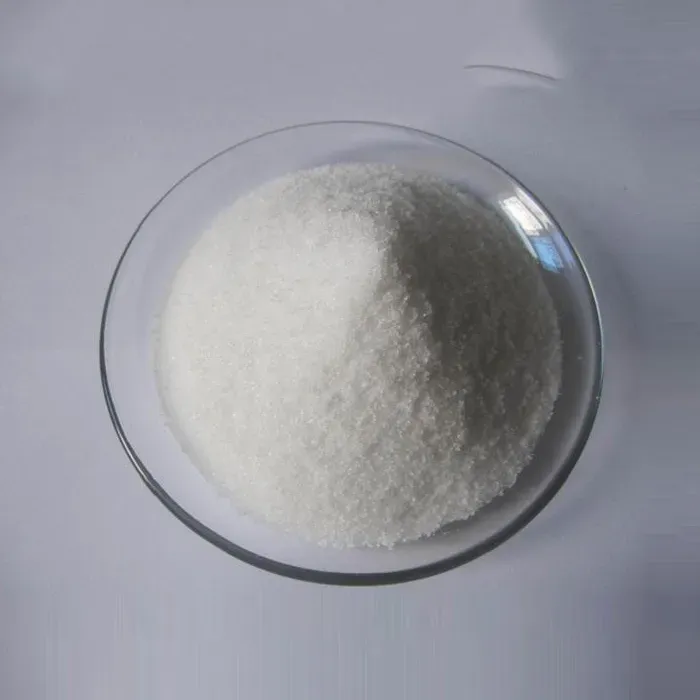
Training and Workforce Empowerment
Achieving Q10% is not solely dependent on technology; workforce empowerment plays an equally critical role. Organizations must invest in training programs designed to educate employees about the importance of quality control and the specific practices that lead to achieving Q10%. A knowledgeable and skilled workforce can identify potential issues on the production line, communicate effectively, and implement practices that uphold quality standards.
Additionally, fostering a culture of quality among employees encourages accountability and pride in their work. When workers understand the impact of their roles on overall product quality, they are more likely to engage in practices that support achieving Q10%. This collaborative approach ensures that every member of the team contributes to meeting and exceeding the established quality standards.
Implications of Q10% for Business Success
The implications of successfully implementing Q10% are profound. Organizations that consistently meet this standard can expect to enhance their market reputation, improve customer satisfaction, and drive profitability. In a competitive landscape, high-quality products differentiate a brand, fostering customer loyalty and repeat business. Furthermore, aligning with Q10% standards can lead to reduced returns and warranty claims, ultimately lowering costs associated with poor quality.
In conclusion, Q10% serves as a crucial metric for organizations striving for excellence in advanced manufacturing. By leveraging technology, empowering the workforce, and maintaining a relentless focus on quality, businesses can not only achieve this standard but also set the stage for sustained growth and innovation. Embracing Q10% is not merely about compliance; it’s about laying a foundation for a culture that values quality as a cornerstone of success.