Boiler Feed Water Chemical Treatment Ensuring Efficiency and Longevity
Boilers are essential components in various industries, providing steam for processes ranging from power generation to manufacturing. The efficiency and longevity of a boiler system significantly depend on the quality of the feed water used. Thus, proper chemical treatment of boiler feed water is crucial to mitigate issues such as corrosion, scaling, and carryover, which can adversely affect the performance and lifespan of the boiler.
Understanding Boiler Feed Water
Boiler feed water is the water supplied to a boiler for the generation of steam. The quality of this water is paramount, as impurities can lead to a range of operational problems. Common impurities in water include dissolved salts, organic compounds, gases, and particulate matter. When these impurities are present in boiler feed water, they can cause scaling on heat transfer surfaces, which reduces efficiency, increases fuel consumption, and may result in overheating and eventual failure of boiler components.
The Importance of Chemical Treatment
Chemical treatment of boiler feed water serves several key purposes
1. Corrosion Control Corrosive elements such as oxygen and carbon dioxide can enter the boiler system and lead to significant wear and tear. Treatment chemicals, such as oxygen scavengers (e.g., sodium sulfite), are added to eliminate dissolved oxygen, thereby protecting metal surfaces from corrosion. Additionally, filming amines can be used to create a protective layer on the internal surfaces of the boiler.
2. Scale Prevention Scale formation occurs when water with high mineral content is heated, leading to the precipitation of salts, primarily calcium and magnesium. These deposits can severely impair heat transfer efficiency. Chemicals like polyacrylate and phosphonates are commonly employed to prevent and control the deposition of scale by keeping minerals in solution.
boiler feed water chemical treatment
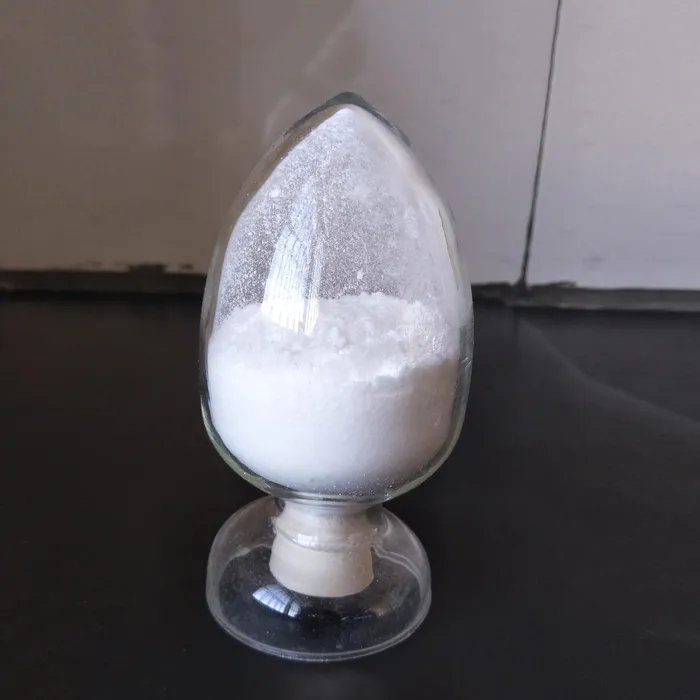
3. pH Control Maintaining an optimal pH level in the boiler water is essential for preventing corrosion. The ideal pH range typically falls between 10 and 12.5. Alkalinity agents such as sodium hydroxide or potassium hydroxide are added to ensure the pH remains within this range, thereby inhibiting the corrosion of boiler components.
4. Sludge Control Sludge can accumulate in the boiler due to the precipitation of suspended solids and impurities. Chemical treatments, including dispersants, can help to keep these particles suspended, enabling them to be removed during blowdown operations.
5. Foam and Carryover Prevention Foaming can occur due to the presence of organic compounds or excessive concentrations of dissolved solids. This can lead to carryover, where water is entrained in the steam, carrying impurities into the system. Anti-foam agents are utilized to minimize foam formation and, consequently, carryover.
Implementing a Treatment Program
The effectiveness of boiler feed water chemical treatment relies heavily on a well-structured treatment program. This typically involves regular testing of feed water and boiler water chemistry to monitor the levels of impurities and adjust the chemical treatment accordingly. Key components of an effective program include
- Water Analysis Regular testing for alkalinity, hardness, total dissolved solids (TDS), and specific contaminant levels is essential. - Customized Treatment Plans Each boiler system is unique, so treatment plans should be tailored based on the characteristics of the feed water and the specific requirements of the steam system. - Continuous Monitoring Utilizing online monitoring systems can provide real-time data, aiding in proactive adjustments to the treatment strategy.
Conclusion
In summary, boiler feed water chemical treatment is vital for the optimal performance, efficiency, and longevity of boiler systems. By implementing a comprehensive treatment program that addresses corrosion, scaling, and other challenges associated with water quality, industries can significantly improve their steam generation processes, reduce operational costs, and enhance the overall reliability of their boiler systems. Establishing a proactive approach to chemical treatment not only safeguards investment in boiler technology but also contributes to sustainable operational practices.