Boiler Feed Water Chemical Treatment Ensuring Efficiency and Reliability
Boilers play a crucial role in various industrial processes, serving as a vital component in power generation, heating, and manufacturing. To ensure optimal performance and extend the lifespan of these systems, proper treatment of boiler feed water is essential. This treatment involves a series of chemical processes designed to address the impurities found in water, thereby preventing damage to the boiler and improving operational efficiency.
Boiler feed water typically contains various impurities, including dissolved solids, oxygen, and carbon dioxide. When these substances enter the boiler, they can lead to several operational challenges, such as scale formation, corrosion, and foaming. Scale, which is primarily composed of salts like calcium and magnesium, can accumulate on the internal surfaces of the boiler and heat exchangers. This buildup reduces heat transfer efficiency, increases fuel consumption, and can ultimately lead to boiler failure if not managed properly.
To combat these issues, a comprehensive chemical treatment program must be implemented. One of the primary steps in this process is the removal of dissolved solids. This can be achieved through various methods, including reverse osmosis and deionization, which effectively purify the water before it enters the boiler. These purification processes help to minimize the concentration of salts and other contaminants, thus reducing the risk of scale formation.
Another critical aspect of boiler feed water treatment is the control of oxygen and carbon dioxide levels. These gases can lead to corrosion, especially in ferrous metals. Oxygen scavengers, such as sodium sulfite or hydrazine, are often added to the feed water to bind with dissolved oxygen. This reaction helps to prevent oxygen-related corrosion, safeguarding the integrity of the boiler system.
boiler feed water chemical treatment
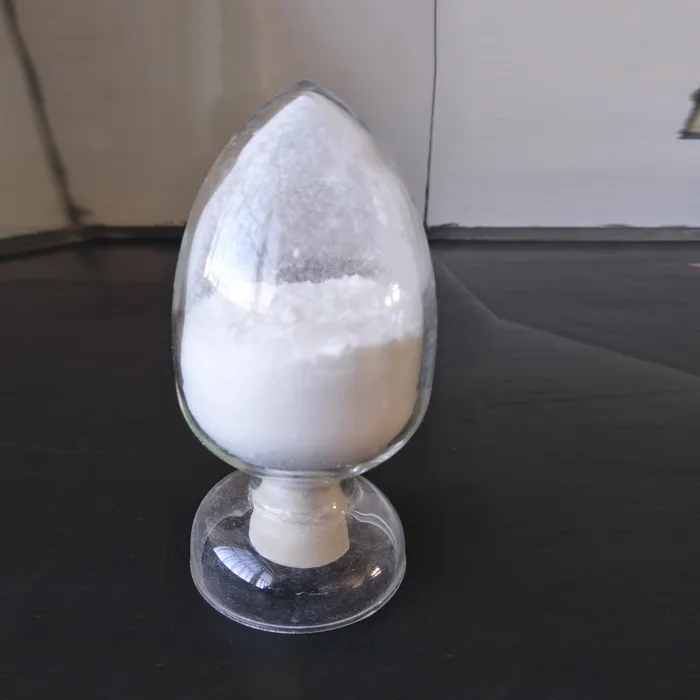
Additionally, the pH level of the boiler water is crucial for preventing corrosion and ensuring that the treatment chemicals work effectively. Maintaining an appropriate pH range usually between 10.5 and 11.5 is important for boiler operation. Alkalinity agents, such as sodium hydroxide or ammonium hydroxide, are commonly used to adjust pH levels and stabilize the chemical environment within the boiler.
In more advanced systems, the use of phosphates can further enhance water treatment. Phosphates serve as scale inhibitors, promoting the formation of more soluble complexes and preventing hard scale formation. They also provide a protective layer on the metal surfaces, reducing direct contact with aggressive water constituents.
Regular monitoring and testing of the boiler feed water quality are imperative for the successful implementation of a chemical treatment program. Parameters such as total dissolved solids (TDS), conductivity, pH, and specific ion concentrations should be routinely analyzed. This ongoing assessment allows for timely adjustments to the treatment chemicals, ensuring that the system operates efficiently and safely.
In conclusion, boiler feed water chemical treatment is vital for maintaining the efficiency and reliability of boiler systems. By addressing the impurities present in feed water through various chemical processes, industries can prevent scale formation and corrosion, extend equipment lifespan, and optimize operational costs. As technologies advance, so does the importance of robust water treatment programs in ensuring sustainable and efficient industrial operations.