Additives for Polymers Enhancing Performance and Functionality
Polymers are ubiquitous materials found in countless applications, from household items to advanced engineering components. However, the intrinsic properties of pure polymers often need enhancement to meet specific performance requirements. This is where additives come into play. Additives are substances incorporated into polymers to improve their processing, physical, mechanical, and aesthetic properties. This article delves into the various types of additives commonly used in polymers and their benefits.
Types of Additives
1. Plasticizers One of the most common classes of polymer additives, plasticizers, are used to increase the flexibility and workability of polymers. They reduce the viscosity of the polymer melt, making it easier to process. Common examples include phthalates and adipates, which are often used in polyvinyl chloride (PVC) products. Adding plasticizers can significantly enhance the flexibility of rigid materials like PVC, making them suitable for a broader range of applications.
Additives for Polymers Enhancing Performance and Functionality
3. Fillers Fillers are added to polymers for a variety of reasons, primarily to reduce production costs and improve mechanical properties. Mineral fillers, such as talc or calcium carbonate, can enhance stiffness and impact resistance. Furthermore, fillers can improve the thermal stability and decrease the permeability of polymers, making them ideal for applications requiring enhanced durability.
additives for polymers
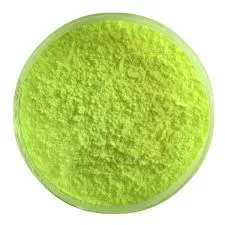
4. Colors and Pigments Aesthetics play a significant role in consumer products, and coloring agents provide a means to achieve desired aesthetics. These additives can be organic or inorganic compounds that impart specific colors to the polymer. Masterbatches—concentrated mixtures of pigments and carriers—are often used for achieving consistent coloration.
5. Flame Retardants With safety being a paramount concern, especially in building and electronic materials, flame retardants are crucial additives. They help reduce the flammability of polymers, slowing down the spread of fire. Halogenated flame retardants, along with non-halogenated alternatives like phosphorus compounds, are commonly employed in various applications to enhance fire resistance.
6. Surfactants and Coupling Agents These additives improve the compatibility and dispersion of different materials in a composite system. Surfactants can lower surface tension, aiding in the mixing of hydrophilic and hydrophobic components. Coupling agents enhance the bond between fillers and the polymer matrix, improving mechanical properties.
7. Antimicrobial Agents With increasing awareness of hygiene, especially in consumer goods, antimicrobial additives have gained prominence. These substances inhibit the growth of bacteria, mold, and fungi, making them particularly valuable in medical applications, food packaging, and household items.
Conclusion
Additives for polymers are essential for enhancing the performance and tailoring the properties of polymer materials to specific applications. As industries evolve and new challenges arise, the demand for innovative additives continues to grow. In the future, research into biobased and environmentally friendly additives may open new avenues for sustainable polymer development. By leveraging the advantages of additives, manufacturers can produce polymers that are not only functional but also cater to the increasingly diverse demands of modern consumers. Ultimately, the integration of additives into polymer science will play a crucial role in advancing technology and improving quality of life.