Boiler Water Chemistry Overview and Importance
Boiler water chemistry plays a crucial role in the efficiency and longevity of conventional and industrial heating systems. Proper management of boiler water is essential to prevent issues such as scaling, corrosion, and system failures, which can lead to costly downtime and repairs.
Understanding Boiler Water Chemistry
Boiler systems rely on water to generate steam or hot water for various applications, including heating, power generation, and industrial processes. The chemistry of the water used in these systems must be meticulously managed to maintain optimal performance. It involves maintaining specific parameters such as pH, dissolved oxygen, total dissolved solids (TDS), hardness, and alkalinity.
Key Parameters
1. pH Level The pH of boiler water is critical as it influences the solubility of various minerals and gases. A pH level between 10 and 11.5 is typically recommended for high-pressure boilers. Maintaining this range minimizes the risk of corrosion and scaling.
2. Dissolved Oxygen (DO) Oxygen in the boiler water can lead to severe corrosion in metal components. Controlling dissolved oxygen levels to below 0.007 ppm through mechanical means, such as deaeration, or through chemical methods, such as oxygen scavengers (e.g., hydrazine, sodium sulfite), is essential.
3. Total Dissolved Solids (TDS) TDS refers to the total concentration of dissolved substances in water. High TDS levels can lead to scale formation on heat transfer surfaces, reducing efficiency. Regular blowdown of the boiler helps maintain optimal TDS levels by removing concentrated water from the system.
4. Hardness Hardness in water is primarily due to calcium and magnesium ions. These ions can precipitate and form scale deposits in the boiler. Softening the water through ion exchange or other chemical treatments is vital to prevent hardness-related problems.
boiler water chemistry pdf
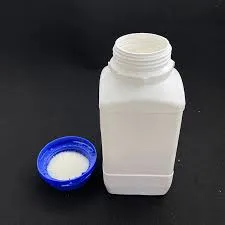
5. Alkalinity Alkalinity, often measured as carbonate and bicarbonate content, helps buffer pH levels in the boiler. Maintaining appropriate alkalinity ensures stability and reduces the risk of corrosion.
Scaling and Corrosion
Two of the most significant issues in boiler water chemistry are scaling and corrosion. Scaling occurs when mineral deposits form on the boiler's heating surfaces, insulating these surfaces and reducing efficiency. Common minerals that contribute to scaling include calcium carbonate, silica, and iron. To mitigate scaling, various treatments—like using scale inhibitors—are employed alongside proper water treatment.
Corrosion, on the other hand, degrades metal components of the boiler. It can lead to leaks, unplanned downtime, and significant repair costs. Corrosion can be exacerbated by dissolved oxygen, acidic conditions, and the presence of salts. Therefore, regular monitoring and chemical treatment are vital to safeguard against corrosion.
Importance of Boiler Water Testing
To maintain the chemistry of boiler water, regular testing is necessary. Laboratories analyze water samples for pH, DO, TDS, hardness, and alkalinity to ensure they meet specified guidelines. Operators need to be trained to understand results and take corrective actions when necessary.
Conclusion
Boiler water chemistry is a complex but essential aspect of managing heating systems. Proper chemistry management not only extends the lifespan of the boiler but also enhances its operational efficiency. By understanding and controlling crucial parameters—such as pH, dissolved oxygen, TDS, hardness, and alkalinity—operators can mitigate the risks of scaling and corrosion, leading to safer and more cost-effective operations. Regular water testing and appropriate chemical treatments are indispensable practices for maintaining optimal boiler performance. As industries increasingly focus on sustainability and efficiency, mastery of boiler water chemistry becomes ever more critical.