Fillers for Polymers Enhancing Performance and Reducing Costs
In the world of polymer manufacturing, fillers play a crucial role in enhancing the properties of base polymers while simultaneously reducing production costs. Fillers are non-metallic materials added to polymers in order to improve various physical and mechanical characteristics, such as tensile strength, durability, and thermal stability. They can also assist in improving processing efficiency and can lead to wasted material reductions, making them an integral part of modern polymer technology.
Types of Fillers
Fillers can be broadly classified into two categories reinforcing fillers and non-reinforcing fillers. Reinforcing fillers, such as carbon black, glass fibers, and aramid fibers, significantly enhance the mechanical properties of polymers. These fillers are primarily used in applications that require increased strength, stiffness, and resistance to wear and fatigue. Non-reinforcing fillers, such as talc, calcium carbonate, and silica, tend to serve more economic functions by reducing costs and improving bulk properties, while only slightly enhancing mechanical performance.
1. Reinforcing Fillers Reinforcing fillers are typically used in industries where the strength and durability of the polymer are critical. For example, carbon black is commonly used in the tire industry to enhance the longevity and wear resistance of rubber products. Glass fibers are employed in thermosetting and thermoplastic matrices to improve their mechanical strength, making them suitable for automotive and aerospace applications.
2. Non-reinforcing Fillers Calcium carbonate is a prevalent non-reinforcing filler used in applications such as packaging and household goods. It reduces costs and adds bulk without significantly compromising the polymer's strength. Talc is another widely used filler, particularly in polypropylene and other thermoplastics, where it improves stiffness, thermal resistance, and surface smoothness.
Benefits of Using Fillers
The incorporation of fillers into polymer formulations offers several advantages. The most notable benefit is cost reduction, as fillers are often less expensive than the base polymer. By substituting part of the polymer with fillers, manufacturers can produce a final product at a reduced cost without significantly affecting the desired properties.
fillers for polymers
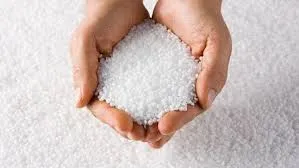
Furthermore, fillers can improve mechanical properties. For instance, adding glass fibers can increase the tensile strength and modulus of a polymer composite, making it suitable for demanding applications. Additionally, fillers can enhance thermal stability, helping to improve the performance of products in high-temperature environments.
Fillers can also aid in processing. By modifying the viscosity of the polymer melt, fillers can enhance the flow characteristics during manufacturing processes such as injection molding or extrusion. This can help in achieving more complex shapes and reducing energy consumption during processing.
Challenges and Considerations
Despite the numerous benefits, the use of fillers also presents some challenges. The choice of filler must be carefully considered, as the type and amount of filler can significantly influence the physical and aesthetic properties of the final product. Overloading a polymer with fillers can lead to brittleness or undesirable surface finishes.
Compatibility between the filler and the polymer matrix is another critical factor. Poor adhesion between the filler and polymer can lead to decreased performance under stress. Therefore, surface treatments or coupling agents are often employed to enhance the interaction between the two phases.
Conclusion
Fillers are indispensable in the polymer industry, providing a balance between performance and cost-effectiveness. Their ability to modify mechanical properties, enhance processing characteristics, and reduce manufacturing expenses makes them an attractive choice for manufacturers across diverse sectors. As advancements in filler technology continue to evolve, we can expect to see even more innovative applications and improvements in the quality of polymer-based products. The challenge remains in selecting the right type of filler to optimize the performance of the polymer without compromising efficiency, sustainability, or final product quality.