Understanding Boiler Water Treatment Chemicals
Boiler systems play a critical role in many industrial processes, including power generation, heating systems, and various manufacturing activities. For these systems to operate efficiently, the water used within them must be treated properly. Improper water treatment can lead to serious problems such as scale formation, corrosion, and fouling, all of which can significantly reduce the efficiency of a boiler system and lead to costly downtime. The use of specialized boiler water treatment chemicals is essential to prevent these issues and ensure optimal operation.
The Importance of Boiler Water Treatment
Water is not just a simple medium in boiler operations; it carries with it a range of impurities that can be detrimental to the functionality and longevity of the boiler. Contaminants such as dissolved salts, silica, and various organic materials can lead to scale build-up on heat exchange surfaces, reducing thermal efficiency. Corrosion, often caused by oxygen and carbon dioxide present in the water, can damage critical components and result in leaks or failures. To combat these challenges, boiler water treatment chemicals are employed to condition the water appropriately before it enters the boiler system.
Types of Boiler Water Treatment Chemicals
1. Corrosion Inhibitors These chemicals are used to protect the metal surfaces of the boiler from oxidative damage. Common corrosion inhibitors include sodium nitrite, molybdate, and phosphate. They work by forming a protective film on the metal surfaces, which minimizes the contact of corrosive agents with the metal.
2. Scale Inhibitors Hardness minerals like calcium and magnesium can precipitate out of the water, forming scale deposits on boiler surfaces. Scale inhibitors, such as polyacrylic acid and phosphonates, help to keep these minerals in solution, preventing scale formation.
3. pH Adjusters Maintaining the correct pH level is vital for preventing corrosion and scaling. Chemicals like caustic soda (sodium hydroxide) are used to elevate pH, while acids like sulfuric or hydrochloric acid can be used to lower pH when necessary.
boiler water treatment chemicals
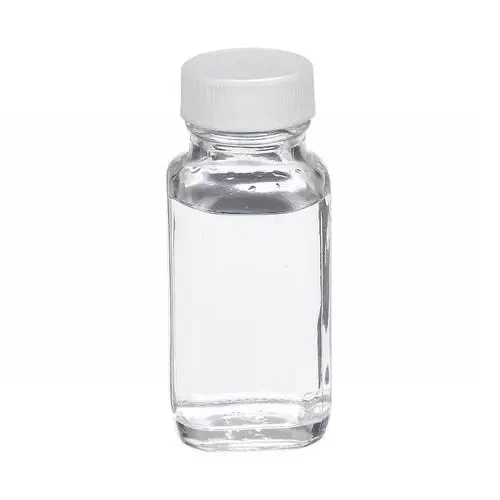
4. Oxygen Scavengers Oxygen is one of the primary causes of corrosion in boiler systems. Oxygen scavengers, such as hydrazine or sodium sulfite, are used to remove dissolved oxygen from the water, thus reducing the risk of oxidative stress on the boiler materials.
5. Biocides Biological growth can occur in boiler feed water, leading to fouling and operational issues. Biocides are used to control microbial growth and maintain water quality. Common biocides include quaternary ammonium compounds and isothiazolinones.
6. Defoamers Foaming can occur in boiler systems, which reduces efficiency and can lead to carryover of water into the steam. Defoamers are added to combat this issue, ensuring smooth operation of the boiler.
Implementation and Monitoring
The successful utilization of boiler water treatment chemicals requires careful implementation and ongoing monitoring. Routine testing of boiler water quality is essential to assess levels of dissolved solids, pH, hardness, and the presence of any contaminants. Based on these assessments, adjustments to chemical dosages must be made to maintain optimal water quality.
Additionally, the chemical compatibility with other systems must be considered to avoid adverse interactions that could compromise the treatment process. Regular maintenance checks and inspections can also aid in identifying potential problems before they escalate into more significant issues.
Conclusion
Boiler water treatment chemicals are indispensable for the efficient and safe operation of boiler systems. By addressing corrosion, scaling, and fouling, these chemicals help maintain thermal efficiency and prolong the life of critical equipment. Understanding the types of chemicals available and their functions can aid in selecting the appropriate treatment program tailored to specific water quality and operational needs. Investing in proper boiler water treatment not only enhances the performance of the system but ultimately contributes to improved energy efficiency and reduced operational costs. Thus, industries relying on boiler systems must prioritize water quality management to ensure reliable and efficient operations.