Understanding Additives Used in Plastics
Plastics have become an integral part of modern life, utilized in various applications ranging from packaging and automotive components to medical devices and electronics. However, the production and performance of plastics often rely on a multitude of additives that enhance their properties, making them more suitable for specific applications. These additives are crucial in tailoring plastics to meet the required standards for durability, flexibility, and appearance. In this article, we will explore the different types of additives used in plastics, their purposes, and some of the potential implications for health and the environment.
Types of Additives
1. Stabilizers One of the most commonly used additives are stabilizers. These are substances added to plastics to improve their resistance to degradation from light, heat, and oxygen. For instance, UV stabilizers protect plastics from photodegradation, which can cause discoloration and loss of mechanical properties when exposed to ultraviolet light. Heat stabilizers, often seen in PVC products, assist in maintaining the integrity of the material when subjected to elevated temperatures during processing.
2. Plasticizers Plasticizers are used to increase the flexibility and workability of plastics, making them more pliable and easier to mold. Commonly used in polyvinyl chloride (PVC), plasticizers reduce the rigidity of the polymers, allowing for applications like flexible tubing, flooring, and various children's toys. However, concerns over the safety of certain plasticizers, such as phthalates, have led to increased scrutiny and the development of alternative, safer plasticizers.
3. Fillers Fillers are added to plastics to improve mechanical properties, reduce production costs, and modify other characteristics such as density. Common fillers include talc, calcium carbonate, and glass fibers. These materials enhance strength, decrease weight, and improve thermal and electrical properties. For instance, glass-filled nylon provides superior strength and stiffness, making it suitable for automotive and industrial applications.
4. Colorants Colorants, including dyes and pigments, are essential for delivering aesthetic appeal to plastic products. These additives ensure that plastics can be produced in a wide variety of colors and finishes, enhancing branding and consumer appeal. Colorants must be chemically stable to prevent fading when exposed to sunlight or other environmental factors.
additives used in plastics
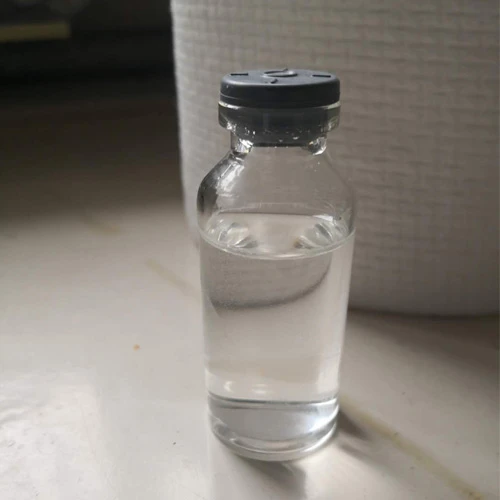
5. Flame Retardants Flame retardants are critical in applications where fire safety is a concern. These additives reduce the flammability of plastics, making them safer for use in electrical appliances, furniture, and automotive parts. However, some flame retardants have been associated with environmental and health concerns, sparking debates about their safety and necessitating the search for less hazardous alternatives.
6. Blowing Agents Used primarily in creating foamed plastics, blowing agents generate a gas within the polymer to create a cellular structure. This process reduces the density of the plastic and improves its thermal insulation properties. Common examples include azodicarbonamide and chemicals that release gases during processing.
Environmental and Health Considerations
While additives play an essential role in enhancing the functionality of plastics, their use can also raise environmental and health concerns. Many additives are subject to regulation due to the potential for leaching into food products or other environments, leading to exposure risks. There is mounting pressure on manufacturers to formulate safer alternatives and for regulatory bodies to establish stringent guidelines to ensure the safety and sustainability of plastic products.
The recycling of plastics can also be affected by the presence of additives. Contaminants introduced by various additives can complicate the recycling process, leading to lower-quality recycled materials. Innovations in recycling technology and the development of bio-based or biodegradable additives are among the responses to these challenges.
Conclusion
Additives are fundamental to the functionalities of plastics, enabling a wide range of applications and enhancing material performance. As the focus on sustainability and health safety grows, it is crucial for manufacturers to adhere to best practices in additive use, ensuring that innovations enhance lives while protecting the environment. Understanding the role and implications of these additives will be key to advancing the plastics industry responsibly in the years to come.