The Role of Plastic Fillers in Modern Manufacturing
In the world of manufacturing and material science, achieving the ideal balance between performance, cost, and sustainability has become increasingly important. To this end, one of the key components used in various applications is plastic fillers. These additives, often overlooked, play a significant role in enhancing the properties of plastics, making them suitable for a wide range of applications.
Plastic fillers are materials added to plastic during the manufacturing process to improve its properties, reduce costs, or enhance its functionality. They can be organic or inorganic and are utilized across various types of plastics, including polyethylene, polypropylene, and polystyrene. Common fillers include calcium carbonate, talc, glass fibers, and clay, each offering unique advantages depending on the intended application.
One of the primary benefits of plastic fillers is their ability to reduce production costs. By replacing a portion of the more expensive polymer resin with a filler, manufacturers can lower the overall material cost of their products. For example, in the production of polyethylene, the incorporation of calcium carbonate can significantly reduce the amount of resin required without compromising the mechanical properties of the final product. This cost-effectiveness is particularly crucial in competitive markets where margins are tight and efficiency is paramount.
In addition to cost benefits, plastic fillers can enhance the mechanical properties of the final product. Fillers can improve strength, stiffness, and durability, making the plastic more suitable for demanding applications such as automotive parts, construction materials, and consumer goods. For instance, glass fibers are often used as fillers to enhance the tensile strength of plastics, allowing them to withstand greater loads and stresses. This improvement in mechanical properties can result in longer-lasting products that require less frequent replacement, contributing to sustainability efforts.
plastic fillers
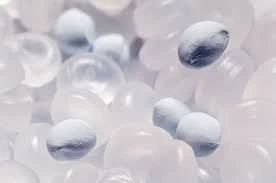
Moreover, plastic fillers can improve thermal and electrical properties, making them suitable for specific applications. Certain fillers can increase the thermal resistance of plastics, enabling them to be used in high-temperature environments. Others may enhance the electrical insulating properties of plastics, making them ideal for electronic components and electrical housings. This versatility allows manufacturers to tailor the properties of their products to meet specific industry standards and consumer demands.
Another essential aspect of plastic fillers is their impact on the processing characteristics of plastics. Fillers can improve the flow properties of molten plastic during manufacturing, facilitating easier processing and shaping into desired forms. This is particularly important in injection molding and extrusion processes, where the ease of flow can significantly affect production efficiency and product quality.
Despite their numerous advantages, the use of plastic fillers is not without challenges. The selection of the appropriate filler is crucial, as it can affect the final material’s performance and appearance. Some fillers may alter the color, texture, or finish of the plastic, which could be undesirable for certain applications. Additionally, the compatibility between the filler and the polymer matrix must be considered to ensure proper dispersion and bonding, which ultimately influences the mechanical integrity of the final product.
As industries increasingly prioritize sustainability, the sourcing and use of fillers have come under scrutiny. Manufacturers are now looking into bio-based fillers derived from renewable resources, such as natural fibers, to reduce their environmental footprint. These sustainable fillers can offer similar benefits to traditional fillers while supporting a greener manufacturing process.
In conclusion, plastic fillers play an integral role in modern manufacturing by enhancing the properties of plastics, reducing costs, and contributing to sustainability efforts. Their versatility and functional benefits make them invaluable in a wide range of applications. As the industry continues to evolve, the development of new and innovative fillers will pave the way for the creation of advanced materials that meet the ever-changing demands of consumers and industries alike. The future of plastic manufacturing, therefore, hinges not only on the polymers themselves but also on the strategic use of fillers to produce high-performance, cost-effective, and sustainable products.