The Role of Fillers in Plastics Enhancing Properties and Reducing Costs
Plastics are ubiquitous in modern society, serving as essential materials across various industries, including automotive, construction, packaging, and consumer goods. One common method to enhance the properties, functionality, and cost-effectiveness of plastic products is the incorporation of fillers. Fillers are inert materials that are added to plastics to improve their mechanical properties, reduce production costs, and enhance specific performance characteristics. This article explores the different types of fillers used in plastics, their benefits, and their impact on the plastic manufacturing industry.
Types of Fillers
Fillers can be broadly classified into two categories reinforcing fillers and extender fillers. Reinforcing fillers, such as glass fibers, carbon fibers, and aramid fibers, significantly enhance the strength, stiffness, and durability of the plastic matrix. These fillers are typically used in applications where mechanical performance is crucial, such as automotive components, aerospace parts, and structural materials.
On the other hand, extender fillers, like calcium carbonate, talc, and clays, are primarily used to reduce material costs while maintaining acceptable performance levels. These fillers have less of an impact on mechanical properties but can improve surface finish, thermal stability, and processability. They are commonly found in products like packaging films, disposable containers, and consumer goods.
Benefits of Using Fillers
1. Cost Reduction One of the most significant advantages of using fillers in plastics is the reduction in material costs. By substituting a portion of the more expensive resin with a filler, manufacturers can decrease production costs without compromising the performance of the end product. For instance, using calcium carbonate as a filler can lead to substantial cost savings in products like plastic sheeting and containers.
2. Enhanced Mechanical Properties Fillers can significantly improve the mechanical properties of plastics. Reinforcing fillers, such as glass fibers, not only increase tensile strength and impact resistance but also improve dimensional stability under varying environmental conditions. This enhancement is critical for applications requiring durability and longevity.
fillers used in plastics
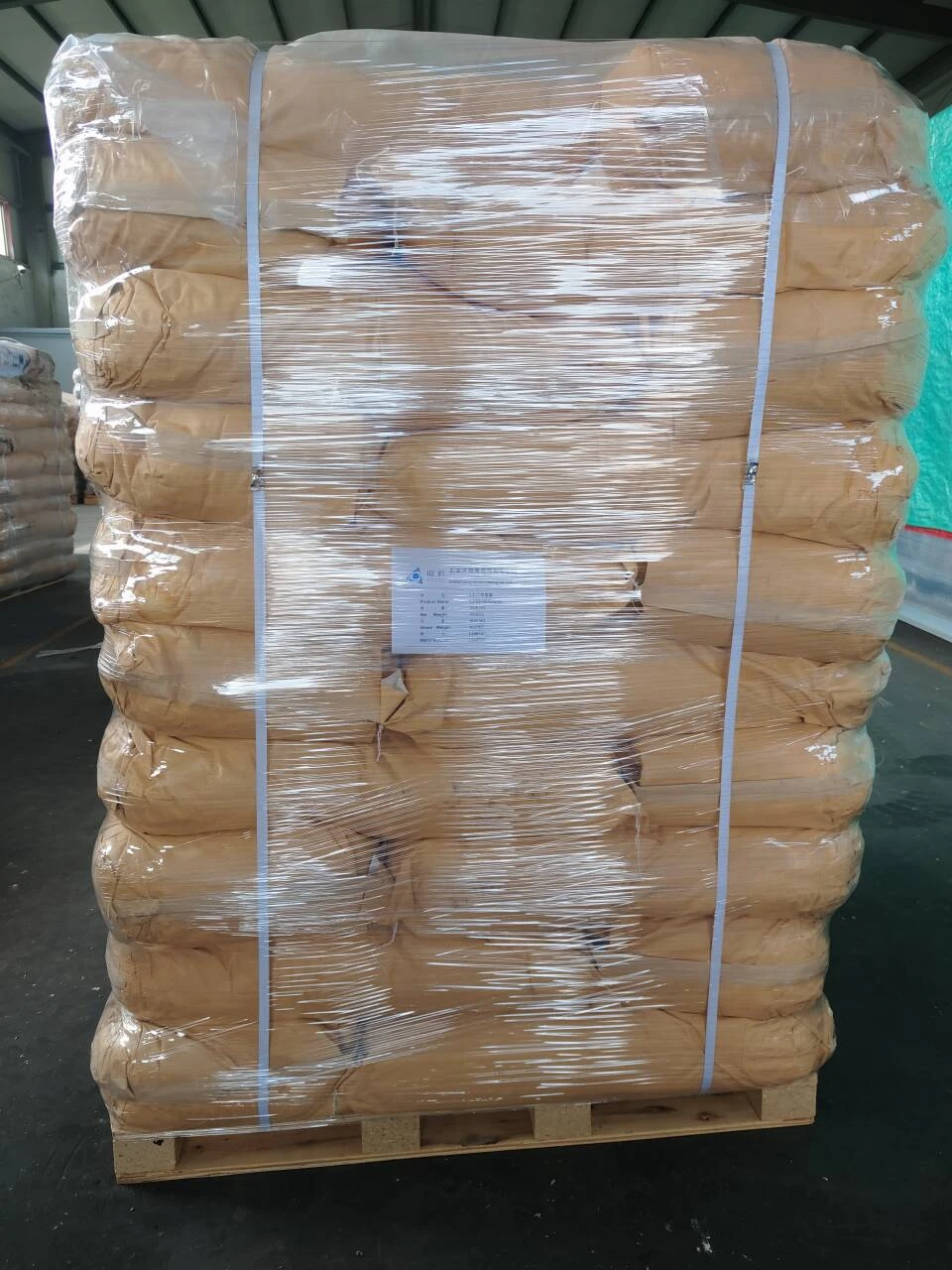
3. Improved Thermal and Flame Resistance Certain fillers can enhance the thermal properties of plastics. For example, adding mineral-based fillers can improve heat resistance, making materials more suitable for high-temperature applications. Additionally, some fillers contribute to flame resistance, which is essential in industries where fire safety is paramount, such as electrical and automotive sectors.
4. Better Surface Characteristics Fillers can be used to refine the surface finish of plastic products. Extender fillers like talc and clay improve the gloss and smoothness of plastic surfaces, making them more aesthetically appealing. This property is particularly important for consumer products, where visual appeal can influence purchasing decisions.
5. Environmental Benefits The use of fillers can also promote sustainability. By incorporating bio-based fillers, such as natural fibers (e.g., hemp, jute), manufacturers can produce biodegradable plastics. These eco-friendly alternatives contribute to reducing plastic waste and enhancing the recyclability of products.
Challenges and Considerations
While fillers offer numerous advantages, several challenges must be addressed. The selection of an appropriate filler depends on the specific requirements of the application, including compatibility with the polymer matrix, processing conditions, and desired end-use properties. Additionally, an excessive amount of filler can lead to decreased performance, such as brittleness or poor flow properties, making it essential to optimize filler loading.
Conclusion
Fillers play a vital role in the plastics industry, offering significant benefits in cost reduction, mechanical enhancement, thermal stability, and surface quality. As the demand for innovative and sustainable materials continues to grow, the strategic use of fillers in plastics will be crucial for meeting evolving consumer and regulatory requirements. By understanding the diverse range of fillers available, manufacturers can create superior plastic products that not only perform well but also contribute to a more sustainable future.