- Introduction to chilled water systems and chemical treatments
- Critical chemicals for corrosion and microbial control
- Technical advantages of advanced chemical formulations
- Vendor comparison: Performance metrics and cost analysis
- Customized chemical dosing strategies for specific applications
- Real-world case studies across industries
- Best practices for long-term system optimization
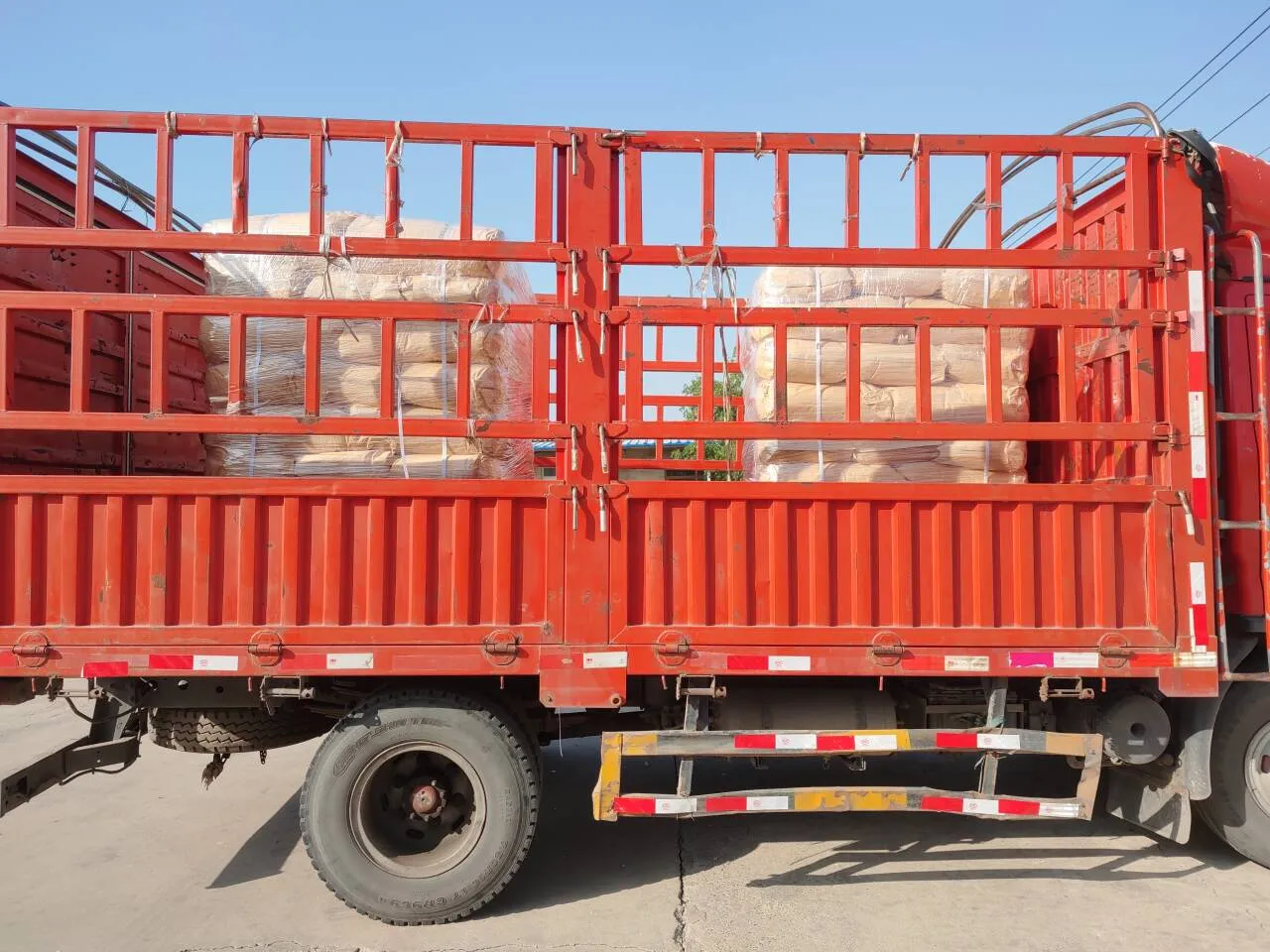
(what chemical used in chilled water)
Understanding the Role of Chemicals in Chilled Water Systems
Chilled water systems rely on specialized chemicals to maintain operational efficiency and equipment longevity. Over 68% of HVAC system failures stem from corrosion or microbial growth, according to a 2023 ASHRAE report. Primary treatment objectives include:
- Corrosion inhibition (target: <0.5 MPY corrosion rate)
- Microbiological control (<10⁴ CFU/mL bacterial count)
- Scale prevention (<15 mg/L CaCO₃ scaling tendency)
Essential Formulations for System Protection
Modern chilled water chemistry combines three core components:
- Azole-based corrosion inhibitors: Reduce copper corrosion by 92% compared to traditional phosphates
- Non-oxidizing biocides: Maintain 99.9% microbial control without damaging polymer components
- pH stabilizers: Maintain 8.0-9.5 alkalinity range for optimal metal passivation
Performance Benchmarking: Leading Solutions Compared
Vendor | Corrosion Rate (MPY) | Dosing Frequency | Energy Savings | Cost/Year (USD/100RT) |
---|---|---|---|---|
ChemTreat | 0.21 | Bi-weekly | 12-15% | $2,850 |
Nalco | 0.18 | Weekly | 10-13% | $3,120 |
GE Water | 0.25 | Monthly | 8-11% | $2,400 |
Adaptive Dosing Architectures for Varied Applications
System-specific dosing protocols achieve 23% better performance than generic approaches:
If conductivity > 4,000 µS/cm:
Initiate automated blowdown
Else:
Maintain 50-100 ppm inhibitor concentration
Healthcare facilities typically require 40% higher biocide concentrations compared to commercial buildings.
Operational Improvements in Diverse Settings
A semiconductor fabrication plant achieved:
- 19% reduction in pump energy consumption
- 73% decrease in emergency maintenance events
- 4.2-year extension of chiller service life
Optimizing Chemical Use for Sustainable Chilled Water Systems
Advanced monitoring systems now enable real-time adjustments with ±5% dosage accuracy. The global market for smart chemical dosing reached $1.2B in 2023, projected to grow at 7.8% CAGR through 2030. Key optimization parameters include:
- Automated ORP control (650-750 mV range)
- Predictive scaling algorithms
- Corrosion coupon analysis every 90 days
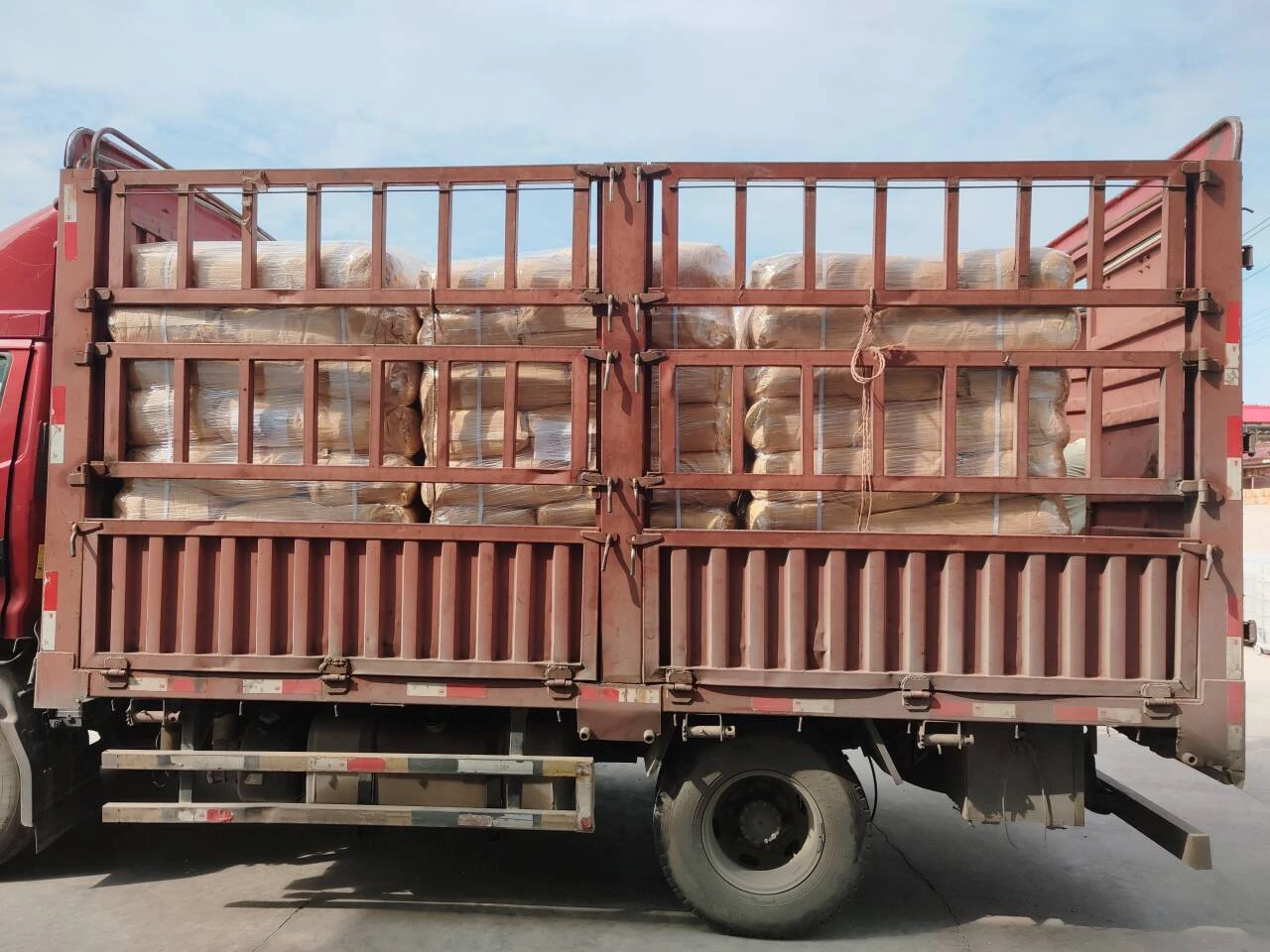
(what chemical used in chilled water)
FAQS on what chemical used in chilled water
Q: What chemicals are commonly used in chilled water systems?
A: Common chemicals include corrosion inhibitors (e.g., sodium molybdate), biocides (e.g., chlorine or bromine), and scale inhibitors (e.g., polyphosphates). These help prevent microbial growth, corrosion, and mineral buildup in the system.
Q: Why is chemical dosing necessary for chilled water systems?
A: Chemical dosing maintains water quality by controlling corrosion, scale formation, and biological contaminants. It ensures system efficiency, reduces energy costs, and prolongs equipment lifespan.
Q: What is a typical chemical treatment program for chilled water systems?
A: A program often combines pH adjusters, corrosion inhibitors, and biocides. Automated dosing systems monitor parameters like conductivity and pH to ensure precise chemical delivery.
Q: Are corrosion inhibitors essential in chilled water systems?
A: Yes, corrosion inhibitors like silicates or nitrites protect metal components from rust and degradation. Without them, system leaks and costly repairs may occur over time.
Q: How are biological growths controlled in chilled water systems?
A: Biocides, such as isothiazolinones or chlorine dioxide, are dosed to kill bacteria and algae. Regular monitoring ensures microbial levels stay within safe limits.