What are Fillers in Polymers?
Fillers are materials added to polymers to enhance their properties, reduce costs, and improve the processing characteristics. In the world of polymers, fillers play a critical role in modifying mechanical, thermal, and aesthetic properties, making them vital in various applications across multiple industries. This article will explore the types of fillers, their functions, and the benefits they bring to polymer materials.
Types of Fillers
Fillers can be broadly categorized into two types inorganic fillers and organic fillers. Inorganic fillers include materials such as talc, calcium carbonate, silica, glass fibers, and clay. These fillers are often chosen for their strength, thermal resistance, and ability to enhance dimensional stability. Organic fillers, on the other hand, include natural materials like wood flour, cotton, and fibers derived from renewable sources.
Functions of Fillers
The inclusion of fillers in polymer formulations serves several important functions
1. Cost Reduction One of the primary reasons manufacturers include fillers is to reduce production costs. By replacing a portion of the primary polymer with a less expensive filler, manufacturers can lower the overall cost of the material without significantly compromising its properties.
2. Improvement of Mechanical Properties Fillers can enhance the mechanical strength and rigidity of polymers. For example, glass fibers are commonly used in epoxy resins to create composite materials that are significantly stronger and stiffer than the base resin alone.
3. Thermal and Electrical Properties Certain fillers can alter the thermal stability of polymers, making them more suitable for high-temperature applications. Moreover, fillers like carbon black are used to enhance the electrical conductivity of certain types of polymers, which is crucial in applications such as electronics and automotive components.
what are fillers in polymers
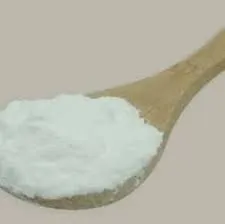
4. Modifying Aesthetic Qualities Fillers can also contribute to the color, texture, and surface finish of polymer products. For instance, titanium dioxide is often added to provide opacity and enhance whiteness in various products.
5. Improved Processing Characteristics Fillers can ease processing by modifying the viscosity of polymer melts, aiding in the manufacturing process. For example, some fillers can reduce the viscosity of a polymer melt, allowing for easier processing through extrusion or injection molding.
Benefits of Fillers in Polymer Applications
The incorporation of fillers offers numerous advantages
- Enhanced Performance Fillers can help improve specific performance criteria depending on the application. For instance, the incorporation of lightweight fillers reduces the overall weight of a polymer product, which is particularly beneficial in the automotive and aerospace industries.
- Sustainability With a growing emphasis on sustainability, the use of natural organic fillers from renewable sources can improve the environmental profile of polymer products. These materials not only reduce reliance on fossil fuels but also contribute to the bio-based content of the final product.
- Versatility Fillers come in various forms and can be tailored to meet specific properties desired in the final product. This versatility makes it possible for manufacturers to create customized materials for niche applications.
Conclusion
In summary, fillers play an essential role in the formulation of polymer materials. By improving mechanical properties, reducing costs, and enhancing the overall performance of polymers, fillers enable the production of a wide range of products that meet specific industry needs. As research continues in the field of materials science, the development of new fillers and technologies promises to enhance the capabilities of polymers even further, paving the way for innovative applications across diverse sectors. Whether for construction, automotive, medical devices, or consumer goods, the strategic use of fillers will remain a fundamental aspect of polymer science and engineering.