Boiler and Cooling Tower Water Treatment Essential Practices for Efficiency and Longevity
Water treatment is a crucial aspect of the operation and maintenance of both boilers and cooling towers in industrial and commercial settings. Proper treatment not only extends the lifespan of these systems but also enhances their efficiency by preventing issues such as scale formation, corrosion, and microbial growth. This article delves into the significance of water treatment in these systems, outlining the primary concerns and essential practices.
Boilers are vital for producing steam or hot water for various applications, while cooling towers are employed to dissipate heat from processes or machinery. Both systems rely heavily on water, making it imperative to manage its quality meticulously. The two main challenges faced in water treatment for boilers include scale deposition and corrosion. Scale, which consists of mineral deposits that form on the heat exchange surfaces, can insulate the heating elements, resulting in lower heat transfer efficiency and increased fuel consumption. Corrosion, on the other hand, can lead to system failures and costly repairs.
To combat scale and corrosion, chemical treatments are commonly employed. These may include the use of water softeners to remove hardness-causing minerals like calcium and magnesium. Additionally, corrosion inhibitors are introduced to protect metal surfaces from oxidizing in the presence of water and oxygen. The selection of appropriate chemicals and their dosages is crucial and must be monitored regularly to ensure optimal results.
boiler and cooling tower water treatment
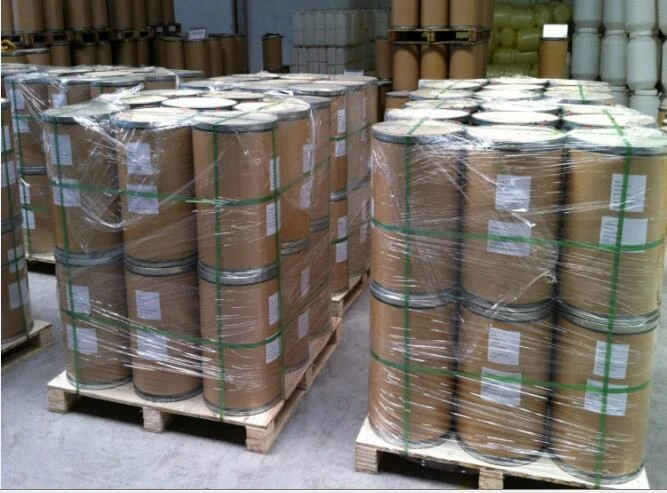
Microbial growth, particularly in cooling towers, presents another significant challenge. These systems can create a suitable environment for bacteria, algae, and fungi, which can lead to biofilm formation, clogging, and even pose health risks such as Legionnaires' disease. To mitigate these risks, biocides are commonly used to control microbial populations. Regular disinfection and monitoring of water quality are essential to maintain a healthy operating environment for cooling towers.
Furthermore, maintaining appropriate water chemistry is vital for the longevity of both boilers and cooling towers. Parameters such as pH, conductivity, and total dissolved solids (TDS) must be regularly tested. For boilers, maintaining a pH level between 10.5 and 11.5 is generally recommended to minimize corrosion. In cooling towers, keeping the pH level slightly alkaline can help in reducing scaling and corrosion as well.
Effective water management practices also include regular blowdown procedures, where a portion of the water is drained to remove impurities and concentrate dissolved solids. This practice is essential for maintaining desired water quality and minimizing operational issues.
In conclusion, boiler and cooling tower water treatment is not merely a regulatory requirement but a critical aspect of system efficiency and longevity. By implementing proper chemical treatments, regular monitoring, and diligent maintenance, operators can significantly reduce the risks associated with scale, corrosion, and microbial growth. Investing time and resources in water treatment ultimately leads to lower operational costs, increased reliability, and prolonged equipment life, making it a necessary component of any industrial or commercial water management strategy.