Chemical Treatment in Cooling Towers
Cooling towers are essential components in many industrial and commercial facilities, allowing for the efficient removal of heat from processes or equipment. However, the effectiveness of a cooling tower can be significantly affected by the quality of the water circulating within it. This is where chemical treatment comes into play. The right chemical treatments not only improve operational efficiency but also prolong the lifespan of the equipment and ensure compliance with environmental regulations.
The primary purpose of chemical treatment in cooling towers is to control scale, corrosion, biological growth, and sludge formation
. Let's delve into each of these aspects in detail.1. Scale Control Scaling is a common problem in cooling towers, primarily caused by the precipitation of minerals present in the water. As water evaporates during the cooling process, dissolved solids concentrate, leading to scale deposits on heat exchange surfaces and other system components. These scale deposits can hinder heat transfer efficiency, causing the system to work harder and consume more energy.
To mitigate scaling, a variety of scale inhibitors are introduced into the cooling water. Common inhibitors include phosphonates and polyacrylic acids, which work by interfering with the crystallization process of scale-forming minerals, allowing them to remain suspended in the water instead of settling on surfaces. Regular monitoring of water chemistry helps to optimize the concentration of these inhibitors, ensuring maximum efficiency.
2. Corrosion Control Corrosion is another significant concern in cooling towers, as metal components are susceptible to oxidative damage. Factors such as dissolved oxygen, low pH, and high temperatures can exacerbate this issue. Corrosive environments can lead to costly repairs and replacements, interrupting operations.
chemical treatment in cooling tower
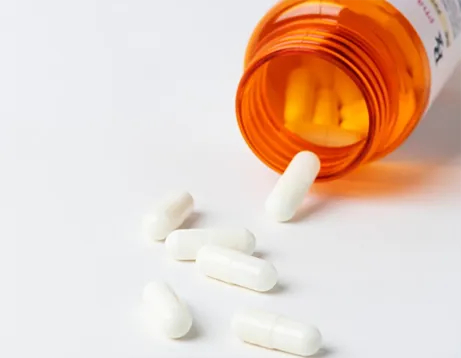
To combat corrosion, anti-corrosive agents are often added to the water. These can include materials like molybdates, which form a protective film on metal surfaces, thereby reducing the rate of corrosion. Moreover, proper water pH management is crucial; maintaining a balanced pH level between 6.5 and 8.5 can significantly decrease the potential for corrosion.
3. Biological Growth Control Biological growth, particularly from algae and bacteria, can clog systems and degrade water quality. Biofouling can lead to increased costs due to decreased efficiency and potential health hazards. For this reason, biocides are regularly employed to manage microbial growth.
There are two categories of biocides oxidizing and non-oxidizing. Oxidizing agents, such as chlorine and bromine, kill bacteria and algae effectively but require careful dosing to avoid damage to system materials. Non-oxidizing biocides, on the other hand, are generally less aggressive but can be more complex, as they often require extended contact times to be effective.
4. Sludge Management Sludge, composed of dirt, debris, and microbial growth, can accumulate in cooling towers, leading to reduced efficiency and foul odors. Regular blowdown—removing a portion of the concentrated water from the system—is a common practice used to control sludge buildup. Additionally, flocculants can be added to help aggregate and settle the solids, facilitating easier removal.
In conclusion, chemical treatment in cooling towers is critical for maintaining system integrity, efficiency, and environmental compliance. By implementing robust water treatment programs — including scaling inhibitors, corrosion inhibitors, biocides, and proper sludge management practices — facilities can ensure that their cooling towers operate at peak performance. Investing in these treatments not only enhances operational reliability but also contributes to significant cost savings in the long term, creating a safer and more sustainable working environment.