The Role of CaCO3 as a Filler in Plastic Composites
Calcium carbonate (CaCO3) has emerged as one of the most widely used fillers in the plastic industry due to its numerous benefits and versatile applications. As a naturally occurring mineral, it is abundant, cost-effective, and offers unique properties that enhance the quality and performance of plastic products. Whether in packaging, automotive components, or household goods, CaCO3 plays a crucial role in the production of various plastic composites.
The Role of CaCO3 as a Filler in Plastic Composites
In addition to cost savings, CaCO3 enhances the physical characteristics of plastics. For instance, it improves tensile strength, impact resistance, and stiffness. These enhanced properties are crucial in applications requiring durable materials that can withstand physical stress. Moreover, CaCO3 contributes to the opacity and whiteness of plastic products, making it an ideal filler for various applications, including film, pipes, and containers.
caco3 filler plastic
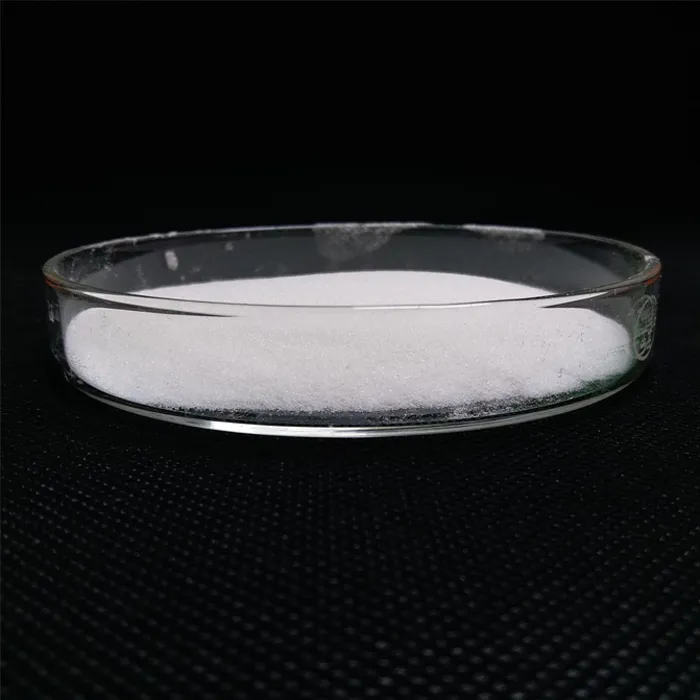
Furthermore, CaCO3 has favorable thermal properties. It can improve the thermal stability of plastics, enabling them to maintain their shape and integrity under elevated temperatures. This characteristic is particularly important for applications exposed to heat, such as automotive parts and electrical housings. Additionally, the addition of CaCO3 can improve the flame retardancy of certain plastic formulations, making them safer for consumer use.
Environmental considerations also come into play when discussing the advantages of CaCO3 fillers. As a natural mineral, CaCO3 is non-toxic and environmentally friendly compared to some synthetic fillers. Consequently, its use aligns well with the growing trend towards sustainable and eco-friendly manufacturing practices. Many consumers and companies, now more than ever, prefer products made with sustainable materials.
However, it’s crucial to note that the effectiveness of CaCO3 as a filler can be influenced by various factors, including particle size, morphology, and surface treatment. These characteristics can affect the dispersion of the filler within the plastic matrix, consequently impacting the mechanical properties of the composite. Manufacturers must carefully optimize these parameters to fully utilize CaCO3 in their formulations.
In conclusion, CaCO3 serves as a vital filler in the plastic industry, offering cost reduction, enhanced physical properties, thermal stability, and environmental benefits. As the demand for high-performance, cost-effective, and sustainable materials continues to rise, the role of CaCO3 is likely to expand further, positioning it as a key player in the future of plastic composites. By leveraging the advantages of this versatile mineral, manufacturers can create innovative products that meet the evolving needs of consumers and industries alike.