Understanding Polyolefin Masterbatch A Comprehensive Overview
Polyolefin masterbatch is an essential component in the world of plastics, serving as a vehicle for colorants, additives, and fillers in the production of various plastic products. Polyolefins, such as polyethylene (PE) and polypropylene (PP), are among the most widely used plastics globally due to their excellent properties, including chemical resistance, flexibility, and durability. This article delves into the definition, applications, benefits, and production processes related to polyolefin masterbatches.
What is Polyolefin Masterbatch?
A masterbatch is a concentrated mixture of pigments and additives encapsulated during a heat process into a carrier resin. Polyolefin masterbatches specifically use polyolefin as the carrier, delivering superior performance and versatility. These masterbatches allow manufacturers to achieve desired colors and properties in their end products with ease, consistency, and efficiency.
Applications of Polyolefin Masterbatch
Polyolefin masterbatches find widespread use in various industries, including packaging, automotive, construction, and textiles. In packaging, they contribute to the aesthetic appeal of plastic films, containers, and bags, allowing for vibrant colors and effective branding. In the automotive industry, these masterbatches improve the appearance and functionality of components, such as dashboards and trim. In construction, they enhance the durability and visual characteristics of materials like pipes and profiles.
Furthermore, polyolefin masterbatches are integral to the production of consumer goods, such as toys and household items. Textile applications also benefit from polyolefin masterbatches, providing color and performance enhancements in non-woven materials and fibers.
Benefits of Polyolefin Masterbatch
polyolefin masterbatch
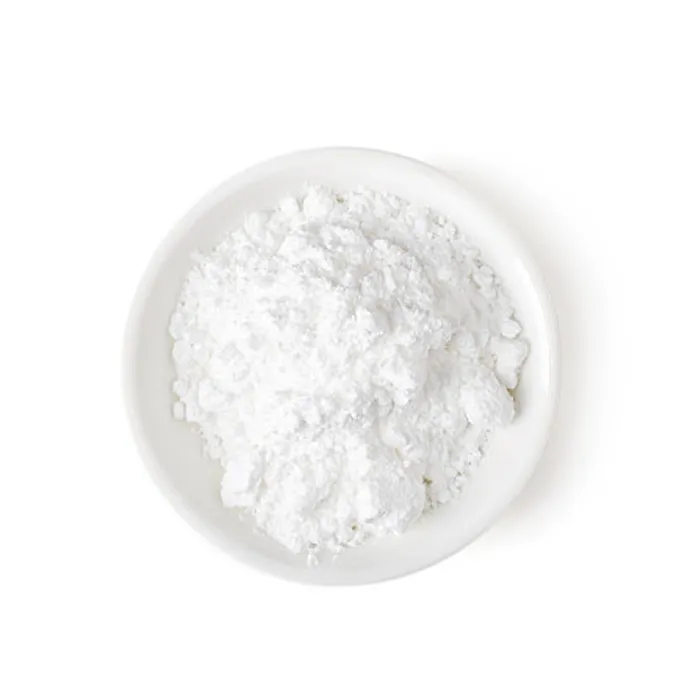
1. Color Consistency and Quality One of the primary advantages of using masterbatches is the ability to achieve consistent color across large production runs, ensuring high-quality outputs.
2. Ease of Use Masterbatches are designed to be easily incorporated into the polymer processing workflow. This simplifies the manufacturing process, reducing the time and effort needed for color matching and adjustment.
3. Cost-Effectiveness By using masterbatches, manufacturers can achieve desired colors without the need for extensive investments in equipment or processes. This can lower overall production costs while maintaining quality.
4. Versatility Polyolefin masterbatches can be customized to include various additives, such as UV stabilizers, anti-oxidants, or flame retardants, making them suitable for a wide range of applications.
5. Environmental Benefits Many manufacturers are now producing biodegradable or recyclable polyolefin masterbatches, catering to the growing demand for sustainable materials in the industry.
Production Process
The production of polyolefin masterbatches involves several steps. First, pigments and additives are selected based on the desired properties of the final product. These components are then blended with polyolefin resin in an extruder, where they are subjected to high temperatures and shear forces. This process ensures that the pigments are evenly dispersed and uniformly integrated into the carrier resin. The resulting masterbatch is then cooled, granulated, and packaged for distribution.
In conclusion, polyolefin masterbatches play a crucial role in the plastics industry, offering a range of benefits from color consistency to production efficiency. Their versatility makes them indispensable in various sectors, enhancing the functionality and aesthetics of countless products. As industries continue to innovate and move towards sustainable practices, the importance of polyolefin masterbatch will undoubtedly grow, paving the way for new applications and advancements in polymer technology.